Цвет автостекла, определение цвета стекла. Определение цвета автостекла
Цвет автостекла, определение цвета стекла
Лобовое стекло – важный элемент конструкции кузова автомобиля. В современных автомобилях стекла надежно вклеиваются в раму, равномерно распределяя нагрузку, которая возникает при эксплуатации автомобиля, за счет этого также увеличивается жесткость кузова.Стекла в автомобилестроении.
Самыми распространенными видами стекол считаются: триплекс и сталинит . Триплекс с латинского означает – тройной. Это трехслойное безосколочное стекло, которое состоит из двух пластин силикатного или органического стекла, между собой они соединены специальным клеевым слоем . Сегодня для производства лобового стекла применяется только триплекс, а что касается сталинита, так его применяют только для стекол боковых и задних. На моделях машин представительского класса стекла выполнены из системы триплекс.Конечно, триплекс стекло значительно дороже, но в тоже время оно безопаснее в эксплуатации, так как при разбитии не образует опасных осколков, которые могут повредить людям в салоне машин. Кроме того стекло такого типа лучше поглощает звук, также немаловажным фактом является то, что при возникновении сколов или трещин его можно отремонтировать. Но при наличии таких преимуществ, есть один весомый недостаток - стекло триплекс легко колется.
Сталинит – это закаленное стекло, оно очень прочное, но в момент разбития образует мелкую крошку, которая осыпается и может поранить человека. В принципе этот вид стела считается безопасным, но все же его не устанавливают на лобовые стекла автомобилей.
Автомобильные стекла, какие они бывают:
- Бесцветные или прозрачные;
- Тонированные – 5% тонировка, которая чуть заметна. Она бывает зеленоватого , бронзового или голубоватого оттенка;
- Атермальные;
- С защитной полосой от ультрафиолетовых лучей. Она так же может быть зеленого, серого или бронзового либо голубого оттенка.
Как определить цвет вашего стекла на автомобиле?
Сделать это достаточно просто, следует поднести с обратной стороны стекла белый лист бумаги, на просвет отлично виден оттенок, который ранее не был замечен. Если же стекло имеет зеленый или голубой или бронзовый оттенок, то стекло в автомобиле тонировано легкой 5% тонировкой. И в этом случае, при замене такого стела следует искать стекло с тем же оттенком, что и на вашем автомобиле было до этого.Атермальное – теплопоглощающее стекло, оно не пропускает тепло в салон автомобиля, это достаточно важный момент, особенно для владельцев автомобилей с кожаными сидениями. Наверное, каждый сталкивался с проблемой нагретого до невозможности сидения. По внешним характеристикам, такое стекло ни чем не отличается от простого стекла.
Шелкография - черная полоса, расположенная по периметру лобового стекла и заднего. Она скрывает место вклеивания стекла к кузову автомобиля.
Тонировка автомашин в настоящее время достаточно актуальна, это одна из вариаций тюнинга автомобиля, при помощи которого можно кардинальным способом изменить его внешний вид. Цвет стекла можно изменить при помощи тонированной пленки, которая наносится на cтекло.
К примеру, у Вас автомобиль черного цвета и он имеет стандартные прозрачные стекла, которые ему совсем не подходят к сформированному образу, в этом случае изменение цвета стекла или фар это одна из возможностей по улучшению внешних данных автомобиля.
Тонирование машин
Сравнительно недавно появилась новое тонирование стекол – арт. тонировка . Эта прекрасная возможность выделится, не слиться с общей массой машин на дороге и ловить на себе толпы взглядов любопытных зевак. Такая тонировка выглядеть радужнее, есть возможность подобрать индивидуально под автомобиль цвет, стиль такой тонировки. Стоимость тонировки, конечно, отличается от простого способа, но не значительно.Тонирование стекол при помощи пленки
Качественная пленка американских производителей состоит из нескольких слоев, что положительно влияет на физические ее качества. С одной стороны покрыта она антиабразивным слоем, который защищает ее от внешних повреждений, а с другой стороны располагается клеевая основа. В основе такой пленки - полиэтилентерефталат – это износостойкое, прочное вещество, кроме того пленка такого качества препятствует проникновению ультрафиолета в салон автомобиля.Cтраница 1
Цвет стекла и интенсивность окраски устанавливаются по соглашению сторон. Стекло, выпускаемое на металлических формах, имеет матовую поверхность.
Цвет стекла зависит также от количества красящего окисла. Закись кобальта, например, при малом ее количестве дает голубое стекло, а при большом - фиолетово-синее с заметным красноватым оттенком.
Цвет стекла: вязан с валентностью металлических ионов, определяемой изме-ениями восприимчивости, например, марганец в восстановлен-шх бесцветных стеклах находится в двухвалентном состоянии. Обычное бесцветное: текло диамагнитно, но если к нему добавить парамагнитную экись, как, например, СоО, то восприимчивость вначале убывает, затем увеличивается до некоторого максимума и, наконец, мед-денно убывает до какого-то постоянного значения.
Цвет стекла зависит также от количества содержав-шегбся-в-нем красящего оксида. Сильное изменение окраски вызывается, кро - шГтого, различным содержанием в стекле отдельных стеклообразующих оксидов. Особенно сильно влияют щелочи (оксид натрия, оксид калия), а также оксед свинца и оксид бора. Оксид меди, например, в известково-натриевом стекле дает голубой цвет, а в цинково-калие-вом - зеленый. Оксид марганца в первом стекле дает красно-фиолетовую окраску, а во втором - сине-фиолетовую. Оксид свинца чрезвычайно усиливает цвет стекла и дает особенно яркие оттенки. Наиболее выразительно окрашиваются свинцово-калиевые стекла. Борная кислота также сильно изменяет цвет окрашенных стекол, однако действие ее в зависимости от красителей различное.
Цвет стекол с коллоидными красителями зависит от размера частиц и от разности показателей преломления стекла и металла.
Цвет стекла согласовывают между изготовителем и потребителем в соответствии с образцом, утвержденным в установленном порядке.
Подбирают одинаковые по цвету стекла и размерам цилиндры, наливают в них по 20 мл воды и при помощи микробюретки приливают 0 1; 0 25; 0 5 и 1 0 мл эталонного раствора Б, 1 мл раствора соляной кислоты, 5 мл раствора сульфаниламида к I мл раствора бромгидрат-этил-а-нафтиламина. Содержимое цилиндра тщательно перемешивают и по истечении 10 - 15 мин сравнивают с испытуемым р / аствором.
По данным В. В. Варгина, цвет стекла в большой мере зависит от его состава. Эмали обычного состава окрашиваются: СоО - в сине-фиолетовый с красноватым оттенком, NiO - от лилового (калиевые составы) до желто-коричневого (натриевые составы), Ct O - в голубой (сине-зеленый), СгОз - в желтый, Сг2Оз - в зеленый, Мг Оз - в красно-фиолетовый, МпО - почти не окрашивает (слабо-желтый), FeO, как СиО, Рб2Оз - в желтый.
Цвет по Сейболту определяют сравнением цвета стандартного стекла с окраской испытуемого продукта, изменяя высоту его столба.
Берут две пробирки, одинаковые по цвету стекла и размерам. В одну из пробирок наливают 20 мл анализируемой кислоты, а в другую 10 мл дистиллированной воды, 3 мл раствора желатина, 2 - 3 капли раствора аммиака (пл.
Стеклянную тару различают по размерам горла, цвету стекла, типу венчика, назначению и конфигурации. По размерам горла ее разделяют на узкогорлую и широкогорлую соответственно с внутренним диаметром горла до 30 мм и выше.
Цилиндры должны быть одинаковыми по размерам и цвету стекла. Растворы в обоих цилиндрах тщательно перемешивают. Затем во второй цилиндр приливают из микробюретки эталонный раствор сульфата титана до получения окраски, одинаковой с окраской испытуемого раствора. При этом объемы раствора в обоих цилиндрах должны быть одинаковыми.
Ускорители процессов стекловарения. Некоторые химически активные вещества, введенные в состав шихты, ускоряют процессы получения стекломассы. В производстве листового, строительного и технических стекол такими ускорителями Являются небольшие добавки сульфата натрия, соединений фтора и хлора - кремнефтори- стого и хлористого натрия, а также нитраты натрия, калия, бария, аммония и другие аммонийные соли.
Кремнефтористый натрий Na2SiF6 (ГОСТ 87-77) - желтоватый порошок, являющийся отходом химического . Он токсичен, разлагается ниже температуры плавления на NaF (фтористый натрий) и газообразный SiF4j сильно летуч: при высокой температуре теряется свыше 30 % фтора. Его обычно вводят в шихту из расчета 0,3-0,5 % фтора сверх основного состава стекла.
Хлористый натрий NaCI. Поваренную соль вводят в шихту в количестве 1,5-3 % ее массы. Подобно фторидам NaCI сильно летуч; при стекловарении теряется по массе до 30-35 % хлорида.
Аммонийные соли вводят в шихту в количестве 0,25- 0,75 % от массы. Они легко летучи и начинают разлагаться с выделением аммиака уже при смешивании шихты. Нитрат аммония NH4N03 плавится при ~ 170°С, его содержание в техническом продукте 98-99 %.
Хлорид аммония NH4C1 и сульфат (NH4)2S04 плавятся при 513-520 °С; их содержание в технических материалах- соответственно 98 и 97 % по массе.
Хорошими ускорителями для реакций в шихтах, а также для осветления расплава являются сульфиды щелочных Me2S и щелочноземельных (MeS) металлов, особенно активны нелетучие сульфиды, содержащиеся в составе доменных шлаков. В качестве ускорителей пригодны стекловидные гранулированные доменные шлаки, содержащие не более 0,4 % Fe203 и не менее 0,5 % сульфидной серы. Их можно вводить в шихты строительного стекла до 9 % массы шихты. В США выпускают фирменный ускоритель «Кэлумайт» - очищенный доменный шлак, содержащий по массе 0,14-0,26 % Fe203 и 0,8-1,15% S-2; его вводят с окислителем - сульфатом натрия, чтобы предотвратить сульфидное окрашивание стекол.
Шлаки являются стойкими ускорителями при высоких температурах варки стекла, характерных для современной технологии. Аналогично ведут себя и химически активные гидрооксиды натрия и калия, которые вводят взамен части карбонатов.
Окислители и восстановители. При получении некоторых видов стекол в шихтах приходится создавать окислительную или восстановительную газовую среду. Такую среду создают для успешного протекания тех или иных реакций, а также для перевода в требуемую валентность соответствующих элементов в составе стекол.
Окислители. Для создания в шихте избытка кислоро-, да при реакциях пользуются окислителями - веществами, разлагающимися с выделением 02. К ним относятся нитраты Na, К и Ва (селитры), небольшие количества сульфатов без восстановителей, а также оксиды мышьяка, сурьмы и церия. В качестве окислителей нитраты вводят в количестве 1-1,5% массы шихты, а оксиды церия, мышьяка и сурьмы - 0,1-0,3% по массе от состава стекла. Сильнее всего действуют окислители с наиболее высокой температурой разложения, например оксид церия и смеси нитратов с оксидами мышьяка и сурьмы.
Нитраты натрия и калия-белые крупнокристаллические соли, получаемые в настоящее время химическим путем. Они легко растворяются в воде и очень гигроскопичны. Технические продукты - селитры натриевая (ГОСТ 828-77Е) и калиевая (ГОСТ 19790-74) - содержат до 99 % основного вещества и разлагаются с выделением оксидов азота и кислорода.
Оксиды мышьяка и сурьмы АвгОз и Sb203 - тяжелые порошки светло-серого и белого цвета, сильно токсичны. Их применяют с нитратами, которые, разлагаясь, окисляют As203 и Sb203 до пентоксидов. Пентоксиды отдают кислород при 1150-1200 °С, т. е. окисляют непосредственно стекломассу.
Диоксид церия Се02 вводят в состав шихты как таковой, а также посредством цериевого концентрата, содержащего 87,4-91,5 % Се02 или нитрата церия Ce(N03)4- ЗН20.
Восстановители. Добавка восстановителей в шихты требуется в тех случаях, когда в них содержится более 4 % общего содержания К20 и RO в виде сульфатов натрия и бария, а также при варке некоторых цветных стекол.
Для восстановления сульфата натрия применяют углеродистые материалы - антрацит, кокс (каменноугольный или торфяной), а также мазут. Твердые восстановители размалывают, просеивают и подают в шихту после предварительного смешивания с сульфатами либо вместе с ними. Мазут распыляют на шихту при ее смешивании. Насыпная плотность молотого угля 800 кг/м3.
В шихтах цветных стекол в качестве восстановителей применяют чистые углеродистые вещества - крахмал, сахар, а чаще всего виннокаменную кислоту С4Н606 и ее кислую калиевую соль КНС4Н402, представляющие собой кристаллические белые порошки, Используют также соединения двухвалентного олова (SnO; SnCI2-2H20) и опилки металлов, не окрашивающих стекло (олово, алюминий) .
Красители. Красителями стекол являются соединения металлов, растворимые в стекломассе (молекулярные красители), или образующие в ней взвешенные микрочастицы металлов и их соединений (коллоидные красители). Окраска, придаваемая стеклам, зависит от природы и концентрации красителей, их валентности, химического состава стекла и условий получения стекломассы.
Молекулярные красители. Для окрашивания листового, строительного и технических стекол чаще всего применяют соединения марганца, кобальта, хрома, никеля и меди. Стекла окрашивают также оксидами железа, но в этом случае получают грязноватую окраску. Поэтому в качестве красителей их применяют только в производстве тарных изделий.
Окраска соединениями марганца зависит от их валентности в стекле. Двухвалентный марганец (МпО) придает стеклам желтоватый цвет, трехвалентный (Мп203) - цвета от розовато-сиреневого до фиолетового. Окраска малоинтенсивна, поэтому для получения яркого цвета оксиды марганца приходится вводить в больших количествах (МпО - 5-6 %, Мп203 - 1-3 %). При вводе 15-20% Мп203 получают черные стекла.
Трехвалентный марганец вводят в шихту природной марганцевой рудой, содержащей пиролюзит Мп02. В техническом продукте содержится не менее 85 % Мп02 и не более 1% Fe203. Главные месторождения - Чиа - турское (ГССР) и Никопольское (УССР).
Технические стекла окрашивают чистым препаратом - марганцевокислым калием КМп04. При нагревании Мп02 и КМп04 разлагаются и выделяют кислород, присутствие которого необходимо для образования Мп203 и получения сиреневой и фиолетовой окраски.
Соединения железа в зависимости от валентности окрашивают стекла в желтоватый (Ре20з) и голубой (FeO) цвета (см. п. 3.4). Как краситель FeO примерно в 10 раз более интенсивен, чем Fe203. Двухвалентное железо (0,3-0,5 % по массе) вводят в стекла для придания им поглощения в инфракрасной области спектра. Оксид железа Fe203 (крокус, мумия) в присутствии ионов серы и восстановителей может образовать сульфиды железа FenSm, которые окрашивают стекла в зависимо
Го сти от концегітраций, в цвета от желто-оранжевого до черного.
Так как в промышленных стеклах всегда имеются примеси оксидов железа, сульфидную окраску обычно получают введением в шихту элементарной серы (0,3- 4 % к массе шихты) или сульфата натрия с избытком восстановителя.
Соединения кобальта чрезвычайно интенсивно окрашивают стекла в синие цвета независимо от условий получения стекломассы. Красители - соединения двухвалентного кобальта (условно СоО), которые вводят в шихту с помощью оксидов С02О3 или СО3О4, получаемых химическим путем в виде порошков черного цвета, переходящих в низшую валентность при 895-900 °С с образованием СоО соответственно 90,4 % и 93,3 % (по массе). Для получения стекла голубого цвета достаточно 0,002 % СоО, для синего и ярко синего - 0,1-0,3% СоО.
Соединения хрома также интенсивно окрашивают стекла в желто-зеленый цвет, а в присутствии окиси меди - в травянисто-зеленый. Красителем является оксид хрома СггОз, который вводят в шихту чаще всего в виде легко растворимых в воде оранжевых кристаллов бихро - мата калия (хромпика) К2СГ2О7. Добавка СГ2О3 обычно составляет 0,25 % - 1,2 % массы шихты. В восстановительных условиях в стеклах могут выделиться корольки металлического хрома.
Соединения никеля придают стеклам разные цвета в зависимости от их концентрации и основного состава стекла. Окраска вызывается двухвалентным никелем (NiO), который вводят в шихту триоксидом Ni203 - тяжелым черным порошком. При малых концентрациях NiO (0,25-0,3%) стекла получают дымчатые, при 2- 3% NiO - красновато-фиолетовые, особенно чистого тона в присутствии КгО.
Из соединений меди молекулярными красителями являются оксид меди СиО и наиболее часто применяемый пятиводный сульфат меди - медный купорос CuS04- 5Н20. Эти соединения придают стеклам голубую, слегка зеленоватую окраску. Медный купорос - крупные кристаллы голубого цвета с содержанием 28,8 % СиО; оксид меди - порошок или гранулы черного цвета. Для окрашивания стекла необходимо 1-2 % по массе СиО. Среда должна быть окислительной во избежание восстановления СиО до коллоидной закисной меди СигО.
Оксиды группы редкоземельных элементов -диоксид церия, оксиды неодима и празеодима, а также оксид ванадия в последнее время применяют для окрашивания декоративных архитектурно-строительных изделий и стеклянных блоков. Диоксид церия Се02 придает стеклам светло-желтую, а в присутствии диоксида титана ТЮ2 - чистую золотисто-желтую окраску, оксид неодима Nd203 - красивую розовато-сиреневую окраску, оксиды празеодима Рг203 и ванадия V205 - светло-зеленую окраску. Окрашивание этими оксидами не зависит от температуры и состава газовой среды печи; количество красителя 0,5-1 % по массе. В качестве красителей применяют чистые оксиды, а также азотнокислые соли и концентраты редкоземельных элементов.
Коллоидные красители. К этому виду красителей относятся соединения, способные образовать в массе стекла взвешенные коллоидально-дисперсные частицы металлов или их соединений, нерастворимые в стекломассе. Цвет, сообщаемый стеклам коллоидными красителями, зависит от состава стекла, природы и концентрации красителей, а также от размеров взвешенных частиц. Для получения требуемой окраски частицы выращивают до нужных размеров путем нагревания изделий при определенных условиях температуры и времени. Термообработку изделий для получения окраски называют «наводкой». К коллоидным красителям относятся закисная медь, соединения серебра, золота, селена, кадмия, сульфиды сурьмы.
Закись меди Cu20 - красно-бурый кристаллический порошок-вводится в количестве 1-3 °/о массы шихты. В присутствии чистых восстановителей (виннокаменной кислоты, закиси олова) и при слабо восстановительной атмосфере печи закись меди образует в стекле коллоидный раствор частиц металлической меди, окрашивающих его после наводки в темно-красный цвет (медный рубин).
Соединения серебра, вводимые в состав стекол до содержания 0,1 % Ag, позволяют окрашивать стекла после наводки в желтый цвет, чистый или с зеленоватым оттенком. Изделия окрашивают серебром в массе или с поверхности. В первом случае применяют 10 %-ный (по массе) раствор нитрата серебра - AgN03 (белые кристаллы, содержащие 63,5 %Ag). Для поверхностного окрашивания берут пасту из смеси глины, охры и хлорида серебра AgCl с 75,25 %Ag. В последнее время
Сблй серебра приобрели важное значение при изготовлении фотохро"мных стекол.
Соединения золота применяют для окрашивания стекол в массе в красные цвета - от розового до пурпурного (золотой рубин). Наиболее яркие и чистые цвета получаются после наводки стекол, содержащих РЬО. Красителем является 10 %-ный (по массе) водный раствор хлорного золота АиСЦ - коричневато-красных кристаллов с содержанием 65 % Аи. Для использования раствор поступает в запаянных ампулах. При окрашивании применяются те же восстановители, что и при получении медного рубина. Для получения розовых стекол достаточно 0,01%, рубиновых - 0,02 % Аи (по массе).
Элементарный селен, введенный в стекло в количестве 0,1-0,2 % по массе, образует в стекле коллоидный раствор розового цвета, получаемый сразу, без наводки. В розовые стекла («розалин») селен вводят с помощью технического препарата - черного порошка, содержащего (по массе) 98 % Se (ТУ 5455-74), а также селе - нистокислым натрием Na2Se03 - легко растворимыми в воде, сильно токсичными белыми кристаллами, содержащими 45,7 % Se. Для получения розалина селен вводят с окислителем (0,1-0,2 % As203).
Если селен применять вместе с солями кадмия - сульфидом CdS и карбонатом CdC03, то стекла, содержащие В203 и ZnO окрашиваются в красные цвета возможно выделяющимися частицами сульфоселенида кадмия CdS-CdSe . Для получения ярко-красного стекла чистого тона (селенового рубина) вводят по массе 0,8- 1,2% Se и 1,3 % CdS или (CdS + CdC03) сверх основного состава стекла. Когда применяется CdC03, CdS заменяют более дешевой элементарной серой: в этом случае для получения рубина берут 0,3-0,8 %Se, 1 - 1,45 % CdC03 и 0,5-1 % S по массе сверх основного состава стекла.
При более высоком содержании (Se + CdS) стекла приобретают темно-красный цвет, а при росте содержания (CdS + CdC03) они становятся оранжевыми. В отсутствии селена (CaS+CdC03) окрашивают стекла в желтый цвет. Соли кадмия поставляются: по ГОСТ 2352-69 (CdS) и 6261-70 (CdC03).
Красивый рубин винно-красного цвета получают одновременным введением селена и оксида неодима, % по массе: (Se - до 0,2; Ш20з - 2-2,5). Восстановителем для селена н солен кадмия является винная кислота (0,04-0,06 %). Для получения рубина используют также сульфиды сурьмы Sb2S3, порошок черного цвета (ОСТ 4835-72) н оранжевую пятнсерннстую сурьму. Их вводят в шихту с восстановителем.
Обесцвечиватели. Для устранения зеленого оттенка, придаваемого стеклу оксидами железа, применяют физические и химические обесцвечиватели (см. п. 3.4).
Физические обесцвечиватели - соединения, придающие стеклу розовато-сиреневые цв. ета, дополнительные к окраске оксидами железа. К ним относятся небольшие количества оксида марганца Мп203 (0,15-0,35 %) и смеси красителей - селена и оксида кобальта (0,005- 0,01 % Se, 0,0001 % СоО) или редкоземельных оксидов церия, неодима, эрбия (0,07-0,1 % Се02; 0,005- 0,007 % Nd203; 0,02 % Er203). Вместо оксидов церия и неодима пользуются также резкоземельными концентратами и азотнокислыми солями этих элементов.
Оксиды марганца и редкоземельных элементов являются также и химическими обесцвечивателями, так как все они разлагаются с выделением кислорода, который переводит оксиды железа в слабоокрашивающую трехвалентную форму, в чем и состоит механизм химического обесцвечивания.
Чисто химическими обесцвечивателями могут быть сильные окислители - смеси нитратов и оксидов мышьяка и сурьмы (по 0,02-0,05 % по массе As203 и Sb203) или диоксид церия (0,1-0,2 %).
Глушители. Материалы, которые придают стеклам свойства рассеивать свет и казаться полупрозрачными (опалесцирующими) или полностью непрозрачными (глушеными), называют глушителями. Они образуют в стекломассе соединения, которые полностью растворяются в ней при высокой температуре, но выделяются при охлаждении расплава в виде капель и частиц, размером примерно 1 мкм, содержащих кристаллы глушителей. Глушение происходит при выработке изделий или при их специальной термической обработке (наводке).
До последнего времени глушителями были главным образом соединения фтора - кремнефториетый натрий и криолит - двойной фторид натрия и алюминия 3NaF-AIF3; последний является отходом производства суперфосфата. Это белый кристаллический порошок, состоящий из 12,8 % А120з, 32,8 % Na20 и 54,4 %F"
(ГОСТ 10561"-73). Для некоторых видов стекол применяют также фториды кальция (природный плавиковый шпат СаИг), магния, аммония. Фториды вводят в состав стекол из расчета 5-8 % по массе F" сверх основного состава стекла. При варке стекла до 50 % фтора может улетучиваться; пары его токсичны, поэтому фтор разрешено вводить только в шихты некоторых технических стекол. Этим стеклам фтор придает необходимые свойства и поэтому не может быть заменен другими глушителями.
В настоящее время нередко вместо фторидов применяют соединения фосфора - фосфаты Са и Na. Они требуют высоких температур варки и выработки стекла и склонны к образованию в стекле при охлаждении крупных видимых кристаллов. В качестве глушителя в последнее время используется также оксид алюминия, механически замешиваемый в готовую стекломассу. Наконец, для глушения используют способность расплавов определенных составов расслаиваться при охлаждении с выделением капель другого химического состава. К ликвации склонны малощелочные стекла при введении, например, В203, а также стекла с высоким содержанием СаО и MgO. В настоящее время этот способ получил промышленное применение (см. п. 15.2). Степень глушения стекол увеличивается с возрастанием концентрации глушителей.
Юрий Кукушкин
Стекло
История стекла уходит в глубокую древность. Известно, что в Египте и Месопотамии его умели делать уже 6000 лет назад. Вероятно, стекло начали изготавливать все же позже, чем первые керамические изделия, так как для его производства требовались более высокие температуры, чем для обжига глины. Если для простейших керамических изделий было достаточно только глины, то в состав стекла необходимо минимум три компонента.
Изделия из стекла так же, как и из керамики, практически не подвергаются атмосферным воздействиям и хорошо сохраняются даже под слоем земли. Эти изделия оказались важнейшими документами далекого прошлого. Они донесли до нас бесценную информацию об уровне культуры и техники древних народов. Благодаря стеклу до нашего времени дошли величайшие художественные произведения различных эпох культуры человечества.
Первый стекольный завод в России был построен в 1636 г. близ г. Воскресенска под Москвой. На нем выдували оконное стекло и стеклянную посуду. Через 30 лет в селе Измайлово, также под Москвой, был построен завод, на котором изготовляли высококачественные стаканы, графины, фляги, рюмки, кувшины и др. Особенно быстро стеклоделие развилось при Петре I. В XVIII в. около Москвы действовало шесть стекольных заводов.
Главный потребитель стекла в настоящее время – строительная индустрия. Больше половины всего вырабатываемого стекла приходится на оконное для остекления зданий и транспортных средств: автомашин, железнодорожных вагонов, трамваев, троллейбусов. Кроме того, стекло используют в качестве стенового и отделочного материала в виде пустотелых кирпичей, блоков из пеностекла, а также облицовочных плиток. Примерно треть производимого стекла идет на изготовление сосудов различного типа и назначения. Это прежде всего стеклянная тара – бутылки и банки. В большом количестве стекло расходуется на изготовление столовой посуды. Стекло пока незаменимо для производства химической посуды. В довольно большом количестве из стекла изготавливают вату, волокно и ткани для тепловой и электрической изоляции.
Относительная дешевизна стеклянных строительных материалов обусловливается широким распространением, а следовательно, доступностью и дешевизной сырья. Расплавленное стекло является удобным материалом для формования в изделия механизированным способом. Стекло хорошо поддается механической обработке. Это также снижает стоимость стеклянных изделий. Стекло пилят так же, как дерево, но для этого в кромку дисковой пилы зачеканивают алмазный или иной твердый порошок. Его можно сверлить обыкновенными стальными сверлами, применяя специальную смачивающую жидкость. Стекло колют на куски при помощи простого инструмента, напоминающего колун для дров, но действующим не ударом, а постепенно нарастающим усилием. Стекло можно обрабатывать на токарном станке резцами из особо твердой стали, вытачивая фигурные колонки так же, как из дерева или металла. Стекло шлифуют и полируют, применяя обычные абразивные порошки, инструменты и методы, давно известные и широко используемые в металлообрабатывающем производстве. Стекло можно сварить из одного кварцевого песка, химическая формула которого SiO 2 . Однако для этого нужна очень высокая температура (выше 1700°C). Получение таких температур в печах промышленного типа связано с большими трудностями. Обычные печи, в которых используются твердое, жидкое или газообразное топливо, для этого не годятся. Для плавления кварцевого песка применяют электрические печи специального устройства или горелки, в которых сжигается водород в токе кислорода. Расплавленный кварцевый песок представляет собой столь густую и вязкую массу, что из нее трудно удалить воздушные пузырьки и придать изделиям нужную форму.
В стекловарении используют только самые чистые разновидности кварцевого песка, в которых общее количество загрязнений не превышает 2...3%. Особенно нежелательно присутствие железа, которое даже в ничтожных количествах (десятые доли%) окрашивает стекло в зеленоватый цвет. Если к песку добавить соду Na 2 CO 3 , то удается сварить стекло при более низкой температуре (на 200...300°). Такой расплав будет иметь менее вязкий (пузырьки легче удаляются при варке, а изделия легче формуются). Но! Такое стекло растворимо в воде, а изделия из него подвергаются разрушению под влиянием атмосферных воздействий. Для придания стеклу нерастворимости в воде в него вводят третий компонент – известь, известняк, мел. Все они характеризуются одной и той же химической формулой – CaCO 3 .
Стекло, исходными компонентами шихты которого является кварцевый песок, сода и известь, называют натрий-кальциевым. Оно составляет около 90% получаемого в мире стекла. При варке карбонат натрия и карбонат кальция разлагаются в соответствии с уравнениями:
Na 2 CO 3 → Na 2 O + CO 2
CaCO 3 → CaО + CO 2
В результате в состав стекла входят оксиды SiO 2 , Na 2 O и CaО. Они образуют сложные соединения – силикаты, которые являются натриевыми и кальциевыми солями кремниевой кислоты.
В стекло вместо Na 2 O с успехом можно вводить K 2 О, а CaО может быть заменен MgO, PbO, ZnO, BaO. Часть кремнезема можно заменить на оксид бора или оксид фосфора (введением соединений борной или фосфорной кислот). В каждом стекле содержится немного глинозема Al 2 O 3 , попадающего из стенок стекловаренного сосуда. Иногда его добавляют специально. Каждый из перечисленных оксидов обеспечивает стеклу специфические свойства. Поэтому, варьируя этими оксидами и их количеством, получают стекла с заданными свойствами. Например, оксид борной кислоты B 2 O 3 приводит к понижению коэффициента теплового расширения стекла, а значит, делает его более устойчивым к резким температурным изменениям. Свинец сильно увеличивает показатель преломления стекла. Оксиды щелочных металлов увеличивают растворимость стекла в воде, поэтому для химической посуды используют стекло с малым их содержанием. В табл. 1 приведен состав (в%) некоторых типичных промышленных стекол.
Таблица 1
Сода – сырье относительно дорогое и имеющее огромный спрос со стороны различных отраслей народного хозяйства. Поэтому в качестве источника Na 2 O при варке стекла используют также природный минерал Na 2 SO 4 . В СССР его огромные залежи имеются на месте бывшего залива Кара-Богаз-Гол (рядом с Каспийским морем). Однако в этом случае варка стекла требует более высоких температур. Кроме того, в шихту необходимо вводить уголь для восстановления серы в соответствии с уравнением
2Na 2 SO 4 + С → 2Na 2 O + 2SO 2 + CO 2
При варке стекла первым плавится оксид щелочного металла, после чего в этом расплаве начинают растворяться зерна кварца и известняка, вступая в химическое взаимодействие. Поэтому чем больше в стекле оксидов щелочных металлов, тем при меньших температурах оно плавится. В Древнем Египте, когда техника получения высоких температур была несовершенна, в стеклоделии преобладали рецепты с повышенным содержанием оксидов щелочных металлов (до 30%) и малым содержанием извести (около 3...5%). В эллинистическую эпоху, с усовершенствованием техники получения высоких температур, содержание оксидов щелочных металлов снижается до 16...17%, а извести повышается до 10%. Естественно, что такие стекла стали более стойкими к воде. В настоящее время варка стекла проводится при температуре 1400...1500°C в течение нескольких часов. Процесс варки стеклоделы делят на три стадии: провар шихты, осветление (удаление «мошки» и «свилей»), студка – осторожное охлаждение.
Мошкой стеклоделы называют мелкие пузырьки газа, распределенные по всей массе стекла. Ее удаление из жидкой массы производят «бурлением» при помощи деревянной чурки или обыкновенного сырого картофеля. Помещенные в жидкое стекло, они дают обильное выделение газов, которые и очищают от мошки всю массу. Ее наличие в изделиях считается браком. Мошка особенно недопустима в оптических стеклах.
Стекольным свилем называют нитеобразные потоки, подобные тем, которые можно наблюдать в процессе растворения сахара в воде при медленном перемешивании. Свиль – это видимая граница двух соседних участков стекольной массы. Наличие свилей свидетельствует о плохой перемешанности стекольной массы при варке, т.е. о его низком качестве.
Охлаждение стекла, а точнее изделия из него проводят медленно, чтобы избежать в нем напряжений. При быстром охлаждении стекла поверхностные слои тела затвердевают и могут иметь температуру, близкую к комнатной, а внутренние части, вследствие низкой теплопроводности, могут иметь температуру до 1000°C. Поскольку внутренние части при охлаждении сжимаются, а наружные уже не уменьшаются в размере, в них возникают высокие поверхностные сжимающие напряжения. Внутренние слои, наоборот, испытывают высокие растягивающие напряжения. Такое стеклянное тело называют «закаленным». Закаленное стекло обладает высокой механической прочностью. Однако у него есть и недостатки. При нарушении поверхностного слоя (например, нанесение царапины), т.е. при нарушении сжимающих и растягивающих сил, закаленное стекло разлетается вдребезги.
При медленном охлаждении стеклянного тела растягивающие и сжимающие напряжения не возникают. Такое стекло называют «отожженным». Мелкие изделия, например столовая посуда, отжигаются (охлаждаются) в течение нескольких часов. Крупные и прецизионные изделия, например линзы астрономических объективов диаметра 1 м и более, отжигаются в течение нескольких месяцев.
Окраску стекла осуществляют введением в него оксидов некоторых металлов или образованием коллоидных частиц определенных элементов. Так, золото и медь при коллоидном распределении окрашивают стекло в красный цвет. Такие стекла называют золотым и медным рубином соответственно. Серебро в коллоидном состоянии окрашивает стекло в желтый цвет. Хорошим красителем является селен. В коллоидном состоянии он окрашивает стекло в розовый цвет, а в виде соединения CdS·3CdSe – в красный. Такое стекло называют селеновым рубином. При окраске оксидами металлов цвет стекла зависит от его состава и от количества оксида-красителя. Например, оксид кобальта (II) в малых количествах дает голубое стекло, а в больших – фиолетово-синее с красноватым оттенком. Оксид меди (II) в натрий-кальциевом стекле дает голубой цвет, а в калиево-цинковом – зеленый. Оксид марганца (П) в натрий-кальциевом стекле дает красно-фиолетовую окраску, а в калиево-цинковом – сине-фиолетовую. Оксид свинца (II) усиливает цвет стекла и придает цвету яркие оттенки.
Бутылочное стекло низкого сорта, как правило, имеет окраску, которая зависит от присутствия в нем ионов Fe 2+ и Fe 3+ . Стекольное сырье трудно очищается от железа и поэтому в дешевых сортах оно всегда присутствует. Ионы Fe 2+ хорошо поглощают лучи света с длиной волны примерно 600 ммк (желтые и красные) и, следовательно, окрашивают стекло в дополнительный голубой цвет. Ионы Fe 3+ поглощают лучи с длиной волны 500 ммк (синие и фиолетовые), окрашивая стекло в желтоватый цвет. Важно отметить, что ионы Fe 2+ в области видимого света имеют удельное поглощение, примерно в 10 раз большее, чем ионы Fe 3+ . Поскольку в стекле одновременно содержатся как ионы Fe 2+ , так и ионы Fe 3+ , они и придают стеклу зеленоватую окраску (бутылочный цвет).
Существуют химические и физические способы обесцвечивания стекла. В химическом способе стремятся все содержащееся железо перевести в Fe 3+ . Для этого в шихту вводят окислители – нитраты щелочных металлов, диоксид церия СеO 2 , а также оксид мышьяка (III) As 2 O 3 и оксид сурьмы (III) Sb 2 O 3 . Химически обесцвеченное стекло лишь слегка окрашено (за счет ионов Fe 3+) в желтовато-зеленоватый цвет, но обладает хорошим светопропусканием. При физическом обесцвечивании в состав стекла вводят «красители», т.е. ионы, которые окрашивают его в дополнительные тона к окраске, создаваемой ионами железа, – это оксиды никеля, кобальта, редкоземельных элементов, а также селен. Диоксид марганца MnO 2 обладает свойствами как химического, так и физического обесцвечивания. В результате двойного поглощения света стекло становится бесцветным, но его светопропускание понижается. Таким образом, следует различать светопрозрачные и обесцвеченные стекла, поскольку эти понятия различны.
Следует также отметить, что окрашенное стекло иногда предохраняет содержимое бутылок от нежелательного фотохимического воздействия. Поэтому окраску бутылочного стекла иногда специально усиливают.
Одним из важнейших свойств стекла является прозрачность. Однако в ряде случаев стеклу специально придают непрозрачность путем его «глушения». Это процесс, в результате которого стекло становится непрозрачным. Вещества, способствующие помутнению стекла, называют глушителями. Глушение происходит вследствие распределения по всей массе стекла мельчайших кристаллических частиц. Они представляют нерастворившиеся частицы глушителя или частицы, выделившиеся из жидкой массы при охлаждении стекла. Эти частицы обычно прозрачны, но их показатель преломления отличается от показателя преломления стекла. Поэтому падающий на них луч отклоняется от прямолинейного направления и стекло перестает быть прозрачным. В далеком прошлом в качестве глушителей стекла использовали костяную муку, содержащую фосфат кальция Ca 3 (PO 4) 2 , а также оксиды олова SnO, мышьяка As 2 O 3 и сурьмы Sb 2 O 3 . В настоящее время для этой цели применяют криолит Na 3 , плавиковый шпат CaF 2 и другие фторидные соединения.
Сильно заглушенное стекло (белого цвета) называют молочным. Для его изготовления чаще всего используют криолит. Молочное стекло используют главным образом для изготовления осветительной арматуры.
Несмотря на то что возраст стеклоделия оценивается в 6 тыс. лет, прозрачное и бесцветное стекло люди научились варить лишь на пороге новой эры. До этого производилось непрозрачное окрашенное в различные тона стекло и из него изготавливались главным образом мелкие изделия: бусы, браслеты, пуговицы, кольца, печатки, шахматные фигуры и др. Стеклодувы античной эпохи начали широко применять холодную обработку стекла: рельефную резьбу, гравировку, шлифовку. Как только было получено прозрачное стекло, стеклоделы стали стремиться изготовить из него оконные пластины. Ученые предполагают, что оконное стекло вначале было цветным. Это объясняется тем, что бесцветное стекло получить было весьма непросто, так как сырье обычно содержит различные примеси, которые придают стеклу окраску. Особенно часто в сырье присутствуют соединения железа. Получение пластин для остекления окон оказалось весьма непростым делом. Изготовление полых изделий довольно сложной формы путем выдувания для человека было более простой задачей, чем получение листового стекла. Эта задача была решена лишь к концу средневековья. При раскопках Помпеи, погребенной под пеплом вулкана Везувия в 79 г. н.э., было установлено, что в очень редких случаях в окна были вставлены пластины стекла, которые были довольно толстыми. По-видимому, тонкое листовое стекло итальянские стеклоделы еще не научились делать.
Считают, что метод выдувания, так же как и способ варки прозрачного стекла, был открыт в период смены летоисчисления. Поводов для его открытия было предостаточно. Для получения высоких температур в металлургии был уже известен способ дутья. При варке стекла, требующей также высоких температур, дутье, в частности, проводилось при помощи легких человека. Для этого использовались длинные и полые тростниковые трубки, конец которых обмазывался глиной. Последнее было необходимо для того, чтобы трубка не загоралась. Таким образом, для открытия метода выдувания стеклянных изделий были созданы все предпосылки. Нужен был только случай, когда конец трубки прикоснется к жидкой стекольной массе. Если это произошло, то, продолжая дуть в трубку, человек должен получить что-то похожее на пузырь. Следующим шагом было помещение выдуваемого «пузыря» в деревянную форму, и полое стеклянное изделие почти готово. Как здесь не вспомнить хорошо известное изречение, что «все гениальное просто».
Вероятно, метод выдувания изделий из стекла был изобретен в различных местах, где культивировалось стеклоделие, примерно в одно и то же время. Однако принято считать, что способ выдувания был изобретен в Александрии в I в. до н.э. На первый взгляд, удивительно, что люди научились делать стеклянные изделия сложной полой конфигурации, но не умели делать листовое стекло. Однако для этого были свои весьма основательные технические затруднения.
Оконное стекло
Впервые оконное стекло, хотя и весьма несовершенное, появилось на рубеже старой и новой эры летоисчисления у римлян. Однако после падения Римской империи секреты его производства были утеряны и в начальный период средневековья в Европе оконного стекла не знали. Естественно возникает вопрос, а что же было в окнах? Часто окна закрывались сплошными деревянными ставнями. В теплые дни они открывались, впуская дневной свет внутрь помещения. В иное время окна закрывались и помещение освещали свечами. В России свечи, которые были дороги, часто заменялись горящей лучиной.
В некоторых дворцах, парадных зданиях и культовых сооружениях в Европе в мелкие ячейки в оконных проемах вставляли пластинки слюды, которые ценились очень дорого. В домах простых людей для этой цели использовались бычий пузырь и промасленная бумага или ткань. В середине XVI в. даже во дворцах французских королей окна закрывались промасленным полотном или бумагой. Лишь в середине XVII в. при Людовике XIV в окнах его дворца появилось стекло в виде маленьких квадратиков, вставленных в свинцовый переплет. Листовое стекло большой площади долго не умели получать. Поэтому даже в XVIII в. застекленные окна имели мелкий переплет. Обратите внимание на реставрированные здания петровской эпохи, например на Меньшиковский дворец в Санкт-Петербурге. Однако вернемся к истокам производства оконного стекла.
Как уже было сказано, римляне научились изготовлять оконное стекло в конце старой эры. Они делали это путем отливки и раскатывания жидкого стекла в форму в виде противня, который изготавливался из глины. Отливки извлекались из формы еще в горячем виде, пока стекло сохраняло пластичность. Таким способом получали оконное стекло толщиной около 10 мм и площадью до 0,5 м 2 . Поскольку прилегающая к форме сторона листа оказывалась шероховатой, то стекло не было прозрачным.
Такое стекло находили при раскопках в западноевропейских колониях Рима, а также на Востоке вплоть до Черноморского побережья. Как уже было отмечено, после распада Римской империи это ремесло пришло в упадок и способ производства был забыт и никогда не возобновлялся. Новый способ производства оконного стекла был разработан несколько столетий спустя, т.е. в средние века. Этот способ принципиально отличался от древнеримского, так как получался не отливкой, а выдуванием. Вначале выдували шар, который раскатыванием на плитке и размахиванием в воздухе превращался в подобие большой ампулы. После отрезания верхней и нижней части получался цилиндр. Последний разрезался вдоль твердым минералом и на раскаленной глиняной плите разглаживался в лист деревянной гладилкой. Стекло получалось довольно тонким, хотя и небольшого размера. Сторона, прилегавшая к плите при разглаживании, также получалась шероховатой, а значит, стекло опять же было непрозрачным.
На территории древнеславянского государства археологи многократно находили фрагменты стеклянных кругов диаметром 200...250 мм с хорошо заделанными кромками. Ученые сходятся во мнении, что эти стеклянные круги служили для остекления окон крупных общественных зданий, например храма Киевской Софии и других церквей домонгольской Руси. Считают, что способ их производства сводился к следующему. В форме выдувался сосуд, похожий на конусообразный графин. Дно этого «графина» обрезалось и кромка завертывалась.
В конце средневекового периода в Европе начали широко применять «лунный» способ изготовления листового стекла. В его основу также был положен метод выдувания. При этом способе вначале выдувался шар, затем он сплющивался, к его дну припаивалась ось, а около выдувательной трубки заготовка обрезалась. В результате получалось подобие вазы с припаянной ножкой-осью. Раскаленная «ваза» вращалась с большой скоростью вокруг оси и под действием центробежной силы превращалась в плоский диск. Толщина такого диска была 2...3 мм, а диаметр доходил до 1,5 м. Далее диск отделялся от оси и отжигался. Такое стекло было гладким и прозрачным. Характерная его особенность – наличие в центре диска утолщения, которое специалисты называют «пупком». Лунный способ производства сделал листовое стекло доступным для населения. Однако на смену ему уже в начале XVIII в. пришел другой более совершенный «халявный» способ, который использовался во всем мире почти в течение двух столетий. По существу, это было усовершенствование средневекового способа выдувания, в результате которого получался цилиндр. «Халявой» называли формируемую массу стекла на конце выдувной трубки. Она доходила до 15...20 кг и из нее в итоге получались листы стекла площадью до 2...2,5 м 2 .
Этот способ позволил получать оконное стекло хорошего качества и относительно недорогое для широких слоев населения. Таким образом, проблема светлого и теплого жилища была разрешена лишь в XVIII в. Это было достигнуто трудом многих поколений стеклоделов в течение двух тысячелетий.
Однако «халявный» способ трудно поддавался механизации, а потребности в оконном стекле росли быстрыми темпами. Поэтому поиски новых способов продолжались и в результате в начале XX в. был внедрен в промышленность механизированный процесс. В основе его лежало наблюдение американца Кларка, сделанное в первой половине XIX в. Оно состояло в том, что если на поверхность жидкого стекла положить железный стержень («приманку»), а затем поднимать его, то стеклянная масса приварится (приклеится) к стержню и потянется за ним в виде полотна. При остывании на воздухе получается стеклянный лист. Однако он получался не с параллельными кромками, а в виде клиновидного полотнища. Следующим шагом на пути разработки механизированного способа было изобретение бельгийца Фурко. Он предложил положить на поверхность расплавленной массы керамический брус («лодочку») с продольной щелью. Керамика легче расплавленной стеклянной массы и потому лодочка плавает на поверхности. Если нажать на лодочку, то расплавленная масса выдавливается из щели. На нее опускают «приманку» и тянут вверх. Если скорость подъема приманки будет равна скорости выдавливания стекломассы, то получится правильное полотнище с параллельными кромками. Дальнейшее завершение решения проблемы носит чисто технический и конструкторский характер – устанавливаются подъемные валики, холодильник и другие приспособления. Толщина листа зависит от скорости подъема и скорости охлаждения листа.
В настоящее время оконное стекло производят по данному способу. Имеется и несколько другой вариант технологического оформления процесса производства листового стекла, который используют в США. В нем вместо лодочки с каждого борта полотна располагается пара роликов, между которыми и проходит полотно. Ролики препятствуют сужению полотна и потому отпадает необходимость в лодочке.
В современном строительстве для остекления общественных зданий, гостиниц и витрин магазинов, а также для авто- и вагоностроения, широко используют стекло толщиной 6...8 мм и даже до нескольких сантиметров. Такое стекло называют зеркальным. Оно изготавливается методом проката с последующей шлифовкой и полировкой. Когда говорят о здании, построенном из стекла и бетона, то имеют в виду именно такое зеркальное стекло.
Из сказанного видно, какими усилиями далось человеку прозрачное стекло. Однако в некоторых деталях промышленного и бытового интерьера необходимо, чтобы стекло, наоборот, было непрозрачным, но пропускало свет. Стекло для таких целей подвергают пескоструйной обработке или грубой шлифовке. В настоящее время с этой же целью изготавливают узорчатое листовое стекло, т.е. имеющее какой-либо рисунок. Его получают прокатом на столах или между вальцами, на которые нанесен рисунок.
Мелкие стеклянные изделия делают матовыми обработкой фтороводородной (плавиковой) кислотой. Последняя взаимодействует с диоксидом кремния, находящимся на поверхности, с образованием летучего тетрафторида кремния SiF 4 в соответствии с уравнением
SiO 2 + 4HF = SiF 4 + 2H 2 О
Вряд ли современный человек может оценить тот комфорт и удобство, которое дает ему прозрачное листовое стекло. Человек рождается в светлом и теплом помещении и принимает это как должное.
Фотохромные стекла
Фотохромные стекла изменяют окраску под действием излучения. В настоящее время получили распространение очки со стеклами, которые при освещении темнеют, а в отсутствие интенсивного освещения вновь становятся бесцветными. Такие стекла применяют для защиты от солнца сильно остекленных зданий и для поддержания постоянной освещенности помещений, а также на транспорте. Фотохромные стекла содержат оксид бора B 2 O 3 , а светочувствительным компонентом является хлорид серебра AgCl в присутствии оксида меди (I) Cu 2 O. При освещении происходит процесс
AgCl – [h ν (свет)] → Ag 0 + Cl 0
Выделение атомарного серебра приводит к потемнению стекла. В темноте реакция протекает в обратном направлении. Оксид меди (I) играет роль своеобразного катализатора.
При интенсивном облучении стекла (в том числе и лабораторного) γ-лучами нейтронами и в меньшей мере α-, и β-лучами также происходит окрашивание стекла (чаще в темные и черные цвета). Это связано с изменением структуры стекла и образования ионов, которые играют роль «цветовых центров». При нагревании стекла до температур, близких к температуре размягчения, окраска исчезает. Иногда подобные стекла используют в качестве дозиметров больших доз излучений.
Витраж
Витраж – это декоративная орнаментальная или тематическая композиция, изготовленная из кусков разноцветного стекла, заполняющая оконный проем. Витраж широко использовался для архитектурного оформления готических храмов. Позже в виде витражей начали выполняться гербы городов в городских ратушах и других зданиях общественного назначения. В подражание этому дворянские дома в виде витражей стали оформлять семейные гербы.
Искусство витража получило развитие в эпоху средневековья и достигло наибольшего расцвета в эпоху Возрождения. Слово витраж происходит от франц. vitre – оконное стекло. Кроме разноцветного стекла использовались стекла, расписанные красками. В качестве последних широко применяли тонкорастертые смеси оксидов металлов (меди, железа и др.) с легкоплавким стеклом. Смеси замешивались на воде, вине или растительном масле и в виде кашицы наносились на стекло. После высыхания расписанное стекло подвергалось обжигу при умеренной температуре. По описанию монаха Теофила в XII в. витражи изготавливались следующим образом. Заранее нарезанные и хорошо подогнанные друг к другу куски цветного стекла обертывались по краям полосками свинца. Обернутые куски раскладывались на столе и плотно подгонялись один к другому, а затем свинцовые перемычки спаивались припоем из сплава олова и свинца. Спаивание проводилось с обеих сторон.
В настоящее время искусство витража начинает возрождаться. Особенно ярко проявляется это в Прибалтике.
Хрусталь, хрустальное стекло
Хрусталь, хрустальное стекло – это силикатное стекло, содержащее различное количество оксида свинца. Часто на маркировке изделия указывается содержание свинца. Чем больше его количество, тем выше качество хрусталя. Хрусталь характеризуется высокой прозрачностью, хорошим блеском и большой плотностью. Изделия из хрусталя в руке чувствуются по массе.
Строго хрусталем называют свинцово-калиевое стекло. Хрустальное стекло, в котором часть K 2 О заменена на Na 2 O, а часть PbO заменена на CaO, MgO, BaO или ZnO, называют полухрусталем.
Считают, что хрусталь был открыт в Англии в XVII столетии.
Кварцевое стекло
Его получают плавлением чистого кварцевого песка или горного хрусталя, имеющих состав SiO 2 . Для изготовления кварцевого стекла требуется очень высокая температура (выше 1700°C).
Расплавленный кварц обладает высокой вязкостью и из него трудно удаляются пузырьки воздуха. Поэтому кварцевое стекло часто легко узнается по заключенным в нем пузырькам. Важнейшим свойством кварцевого стекла является способность выдерживать любые температурные скачки. Например, кварцевые трубы диаметром 10...30 мм выдерживают многократное нагревание до 800...900°C и охлаждение в воде. Брусья из кварцевого стекла, охлаждаемые с одной стороны, сохраняют на противоположной стороне температуру 1500°C и потому используются в качестве огнеупоров. Тонкостенные изделия из кварцевого стекла выдерживают резкое охлаждение на воздухе от температуры выше 1300°C и потому с успехом используются для высокоинтенсивных источников света. Кварцевое стекло из всех стекол наиболее прозрачно для ультрафиолетовых лучей. На этой прозрачности отрицательно сказываются примеси оксидов металлов и особенно железа. Поэтому для производства кварцевого стекла, идущего на изделия для работы с ультрафиолетовым излучением, предъявляются особо жесткие требования к чистоте сырья. В особо ответственных случаях кремнезем очищается переводом в тетрафторид кремния SiF 4 (действием плавиковой кислоты) с последующим разложением водой на диоксид кремния SiO 2 и фтороводород HF.
Кварцевое стекло прозрачно и в инфракрасной области.
Ситаллы
Ситаллы – стеклокристаллические материалы, получаемые регулируемой кристаллизацией стекла. Стекло, как известно, – это твердый аморфный материал. Его самопроизвольная кристаллизация в прошлом приносила убытки на производстве. Обычно стекломасса довольно стабильна и не кристаллизуется. Однако при повторном нагревании изделия из стекла до определенной температуры стабильность стекломассы снижается и она переходит в тонкозернистый кристаллический материал. Технологи научились проводить процесс кристаллизации стекла, исключая его растрескивание.
При производстве изделий из стеклокристаллических материалов сначала формуют стеклянные изделия, которые повторным нагреванием подвергают направленной кристаллизации.
Ситаллы обладают высокой механической прочностью и термостойкостью, водоустойчивы и газонепроницаемы, характеризуются низким коэффициентом расширения, высокой диэлектрической проницаемостью и низкими диэлектрическими потерями. Они применяются для изготовления трубопроводов, химических реакторов, деталей насосов, фильер для формования синтетических волокон, в качестве футеровки электролизных ванн и материала для инфракрасной оптики, в электротехнической и электронной промышленности.
Прочность, легкость и огнестойкость обусловили применение ситаллов в жилищном и промышленном строительстве. Из них изготавливают навесные самонесущие панели наружных стен зданий, перегородки, плиты и блоки для внутренней облицовки стен, мощения дорог и тротуаров, оконные коробки, ограждения балконов, лестничные марши, волнистую кровлю, санитарно-техническое оборудование. В быту с ситаллами чаще встречаются в виде белой непрозрачной жаростойкой кухонной посуды. Установлено, что ситаллы выдерживают около 600 резких тепловых смен. Изделия из ситаллов не царапаются и не прогорают. Их можно снять с плиты в раскаленном до красна состоянии и опустить в ледяную воду, извлечь из холодильника и поставить на открытое пламя, не опасаясь растрескивания или разрушения.
Ситаллы – один из видов стеклокристаллических материалов, которые ведут свою историю всего лишь с 50-х годов текущего столетия, когда был выдан на них первый патент.
«Безопасные» стекла
Вероятно, каждому городскому жителю довелось видеть на автотранспорте разбитое лобовое стекло. Первым из «безопасных» стекол, примененных для остекления автомобилей, был триплекс. Он и в настоящее время несет свою службу. При ударе на триплексе образуются многочисленные радиальные и концентрические трещины, но не осколки. Это резко снижает возможность ранения осколками стекла пассажиров. Триплекс состоит из пакета, образованного из двух или более листов обыкновенного стекла, между которыми проложена прозрачная пластичная пленка, прочно соединенная со стеклом склеивающим составом. Благодаря прочной склейке образующиеся при ударе осколки удерживаются на прокладке. Наиболее широко распространенным является трехслойный триплекс. В качестве органической прокладки в нем используют целлулоид. Его изготовление включает следующие операции: стекла покрываются с одной стороны раствором желатина в воде и высушиваются, целлулоидная прокладка обрабатывается с двух сторон дигликолево-спиртовым составом, собранный пакет помещается в вакуум, а затем подогревается до 100°C и прессуется в автоклаве при давлении около 15 атм. Заключительной операцией после обточки абразивными кругами является шпаклевка кромок триплекса смолистыми составами, предотвращающая действие воды на желатин и расслаивание изделия.
В промышленном строительстве широко применяют «армированное» стекло, внутрь которого введена металлическая сетка. Это стекло также может быть отнесено к безопасным, так как при ударе его осколки не рассыпаются, а удерживаются сеткой. «Армированные» стекла обладают противопожарными свойствами, поскольку задерживают развитие пламени в помещениях. Это происходит потому, что от пламени такие стекла не высыпаются из рамы, а лишь растрескиваются. В результате они препятствуют образованию сквозняков, раздувающих огонь.
Пеностекло
Пеностекло – пористый материал, представляющий собой стеклянную массу, пронизанную многочисленными пустотами. Оно обладает тепло- и звукоизоляционными свойствами, небольшой плотностью (примерно в 10 раз легче кирпича) и высокой прочностью, сравнимой с бетоном. Пеностекло не тонет в воде и потому используется для изготовления понтонных мостов и спасательных принадлежностей. Однако его главная область применения – строительство. Пеностекло является исключительно эффективным материалом для заполнения внутренних и наружных стен зданий. Оно легко поддается механической обработке: пилением, резанием, сверлением и обтачиванию на токарном станке.
Для изготовления пеностекла используют стеклянный бой и различные отходы стекольного производства. К ним добавляют пенообразователи, которые образуют газы при высокой температуре: кокс, мел и др. Стеклянный бой и пенообразователи подвергаются тонкому измельчению и хорошо перемешиваются. Смесь помещается в железные формы и нагревается в печи до 700...800°C, при которых пылинки стекла спекаются и образуют полости. При дальнейшем повышении температуры пенообразователи приводят к образованию газов, растягивающих стеклянные полости (процесс вспенивания). Затем следует довольно резкое охлаждение, в результате чего вязкость стекольной массы повышается, пена становится устойчивой и при дальнейшем охлаждении окончательно закрепляется.
Стеклянная вата и волокно
При нагревании стекло размягчается и легко вытягивается в тонкие и длинные нити. Тонкие стеклянные нити не имеют и признаков хрупкости. Их характерным свойством является чрезвычайно высокое удельное сопротивление разрыву. Нить диаметром 3...5 мкм имеет сопротивление на разрыв 200...400 кг/мм 2 , т.е. приближается по этой характеристике к мягкой стали. Из нитей изготавливают стекловату, стекловолокно и стеклоткани. Не трудно догадаться об областях использования этих материалов. Стекловата обладает прекрасными тепло- и звукоизоляционными свойствами. Ткани, изготовленные из стеклянного волокна, обладают чрезвычайно высокой химической стойкостью. Поэтому их применяют в химической промышленности в качестве фильтров кислот, щелочей и химически активных газов. Вследствие хорошей огнестойкости стеклоткани применяют для пошива одежды пожарных и электросварщиков, театральных занавесей, драпировок, ковров и т.п. Стеклоткани кроме огнестойкости и химической стойкости обладают также высокими электроизоляционными свойствами.
Переработка в стекловату осуществляется продавливанием стекломассы через термостойкую пластину с многочисленными отверстиями («фильерами»). Вытекающие через фильеры нити захватываются вращающимся барабаном, наматываются на него и растягиваются. Растяжение нити (утоньшение) зависит от скорости вращения барабана. Роль барабана иногда играет вращающийся диск, на который падает нить.
Существует и принципиально иной способ вытягивания нитей: на вытекающие из фильер нити направляется струя пара или сжатого воздуха. Стеклянные нити растягиваются и в спутанном состоянии образуют войлок.
Стеклопластики и стеклотекстолиты
Первыми называют материалы, получаемые путем горячего прессования стекловолокна, перемешанного с синтетическими смолами. В качестве смол чаще всего используют полиэфирные, фенольные, эпоксидные и карбамидные. В стеклопластиках стекловолокно играет роль армирующего материала, придающего изделиям высокую механическую прочность при малой плотности. Они успешно конкурируют с алюминием и сталью.
В строительстве стеклопластики (волнистые и плоские) применяют для покрытия крыш и для устройства внутренних перегородок. В судостроительной промышленности из них делают корпуса лодок и катеров, в электротехнической их применяют для изготовления аккумуляторных батарей, а в угольной – для труб и призабойных стоек. В некоторых странах из них изготавливают кузова автомобилей, не подвергающиеся коррозии. Стеклопластики на основе стеклянных тканей называют стеклотекстолитами. Их получают пропиткой теми же смолами стеклотканей. Затем заготовки сушат, разрезают на куски определенного формата, собирают в пакеты и прессуют под давлением.
Стеклопластики изготавливают также на основе нетканых стекломатериалов. По сравнению со стеклотекстолитами последние имеют меньшую прочность на разрыв. Эти материалы идут на изготовление облицовочных изделий, жесткой кровли, стеклошифера, стекло-черепицы, оконных проемов.
Посуда из стекла
Качество посуды зависит от состава стекла, способа ее выработки и характера декоративной обработки. Самым дешевым стеклом является кальциево-натриевое. Для посуды улучшенного качества используют кальциево-натриево-калиевое стекло, а для посуды высших сортов – кальциево-калиевое. Самые лучшие сорта посуды изготавливают из хрусталя.
Посудные изделия вырабатывают выдуванием или прессованием. Выдувание, в свою очередь, бывает машинным и ручным. Способ выработки, естественно, отражается на качестве посуды. Сложные по форме и художественные изделия изготавливают только ручным способом. Прессованные изделия легко отличаются от выдутых характерными мелкими неровностями на поверхности, в том числе и на внутренней. На выдутых изделиях они отсутствуют.
Декоративная обработка посуды подразделяется на матирование, гравирование, травление и шлифовку.
Матирование заключается в нанесении матового рисунка при сохранении блестящего фона и реже, наоборот, создании матового фона, а рисунок создается блестящими частями изделия. Для матирования поверхности используют пескоструйные аппараты, в которых создается струя сухого песка. Песчинки оставляют на поверхности мелкие сколы и царапины, которые и придают ей матовый вид, превращая блестящую поверхность изделия в непрозрачную. Для защиты части поверхности от струи песка используют шаблоны, которые накладывают на поверхность изделия. Их изготавливают из резиновых или цинковых листов.
Гравирование изделий проводят при помощи медных вращающихся дисков диаметром 2...10 мм, на которые подается масло с наждачным порошком. Простые рисунки наносят на стеклоизделия при помощи машин посредством пульсирующего нажимания на поверхность специальными иглами. Такие машины по заданной программе могут обрабатывать одновременно четыре-шесть и более изделий.
Травление изделий проводят фтороводородной кислотой. Они предварительно покрываются предохранительным слоем мастики, состоящей из смеси стойких к фтороводородной кислоте веществ (воск, парафин, битум, канифоль). По слою мастики с помощью металлической иглы прорезается рисунок, обнажающий поверхность стекла, подлежащего травлению. Далее изделие помещают на 20...30 мин в травильную ванну, заполненную фтороводородной кислотой или ее смесью с небольшим количеством серной кислоты. В зависимости от концентрации травильного раствора рисунок может быть блестящим или матовым. При использовании газообразного фтороводорода рисунок всегда получается матовым.
После завершения процесса травления изделия промывают водой, а затем для снятия защитной мастики нагревают паром или помещают в ванну с горячей водой.
Декоративная шлифовка основана на удалении части стекла с поверхности изделия. Она бывает поверхностная (валовая) и глубокая (алмазное гранение).
При валовой шлифовке создают на поверхности изделия срезы в виде кружков и овалов, а также нарезают на округлой поверхности плоские грани (обычно не по всей высоте, а на некоторой ее части). Их нарезают при помощи вертикальных кругов из естественных камней или из искусственных наждачных корундовых материалов. Вышлифованное место получается матовым и для восстановления прозрачности на нем проводится полировка на пробковых, деревянных (тополевых) или войлочных кругах.
Алмазному гранению подвергается главным образом хрустальная посуда. Это гранение заключается в прорезании глубоких клинообразных канавок, которые создают пучки лучей, звездочек и других фигур.
Глубокое гранение проводят на корундовых кругах. Круги с алмазной крошкой позволяют резко увеличить скорость резания. Однако у специалистов и ценителей хрусталя изделия, обработанные алмазным инструментом, ценятся ниже, чем обработанные корундовым. Часто для удешевления обработки изделия прессуют, а затем по углублениям проходят резцом. Естественно, такое изделие ценится гораздо ниже.
После алмазного гранения изделие подвергают шлифовке. Однако иногда канавки алмазной грани оставляют матовыми. Вкусы покупателей различны и стеклоделы должны учитывать это.
Благодаря алмазному гранению изделия приобретают особый блеск и дают игру света, особенно при искусственном освещении. Глубокой шлифовке можно подвергать изделия достаточной толщины. Поскольку хрустальное стекло характеризуется большой вязкостью и быстро охлаждается, выдуваемые из него изделия чаще всего имеют толстые стенки. Такие изделия хорошо поддаются алмазному гранению.
Алмазное гранение и поверхностная шлифовка особенно эффективны на изделиях из многослойного цветного стекла. Срезы обнажают нижележащие слои и в результате получается узор различной окраски.
Стекло представляет собой аморфную (не кристаллическую) очень густую массу. Её получают спеканием различных солей металлов. Главным образом, в химический состав стекла входят соли щелочных, щелочноземельных металлов (Na, K) и их оксиды . Обычный речной песок состоит из этих же оксидов металлов и некоторых неметаллов, например в состав кварцевого стекла входит оксид кремния SiO 2 Обычное оконное стекло - это силикат состава Na 2 O CaO 6SiO 2 .
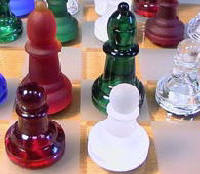
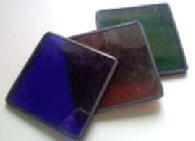
Иногда в стекле возникают области кристаллизации, что приводит к потере прочности. Получают стекло сплавлением кварцевого песка SiO 2 , известняка СаСО 3 и соды Na 2 CO 3 :
Процесс осуществляют в печах при температуре 1100-1600 °С, после чего образовавшуюся стекломассу постепенно охлаждают. Обычное стекло размягчается при температуре 500-600 °С. Есть ещё так называемое природное стекло , которое носит название "обсидиан". Это вещество широко применяется в ювелирных украшениях.
В технике и медицине широко применяется кварцевое стекло .В отличии от обычного оконного оно пропускает ультрафиолетовые лучи.
Образуется при быстром охлаждении расплавленного кварца (кристаллического диоксида кремния SiO 2). обладает химической стойкостью и благодаря этому свойству применяется для изготовления лабораторной посуды. Кварц почти не расширяется при нагревании, поэтому, если раскалённое докрасна кварцевое стекло охладить под струёй холодной воды, то оно не растрескается.
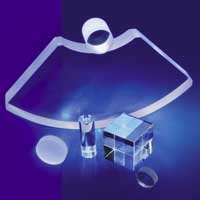
Температуры плавления, которая характеризует тела кристаллического строения, у стекла не существует: размягчение по мере повышения температуры происходит постепенно. Вещества с подобными свойствами так и называются - стеклообразные или просто стёкла.
Доказательством того, что стекло - это очень вязкое аморфное тело, может служить замер толщины Вашего окна, который при желании можете провести дома. Попробуйте, замерьте его по толщине сверху и снизу, - если оно достаточно старое, то окажется не одинаковым (стекает вниз).
Вязкость стекла . Само понятие вязкость свойство жидкости (или газа) оказывать сопротивление перемещению отдельных слоёв друг относительно друга, а также перемещению твёрдого тела, помещённого в жидкость. В Международной системе единиц (СИ) вязкость имеет размерность Па с, но на практике распространена внесистемная единица вязкости пуаз (П): 1 П = 0,1 Па с. Она названа в честь французского физика Жана Луи Пуазейля (1799-1869). Оценки, основанные на определении вязкости разогретых выше 500 °С стёкол, дают для 20 °С значение 1021 П. Для сравнения: вязкость воды при 20 °С равна 0,01 П, глицерина - 15 П, смолы - примерно 108 П. Вязкость стекла по сравнению, например, со смолой - в 10 трлн. раз более вязкая жидкость, чем смола.
Стекло трудно однозначно отнести к одному из двух состояний материи - жидкому или твёрдому. Оно обладает свойствами твёрдых веществ, но в то же время имеет структуру жидкостей. Почему же при расплавлении и последующем охлаждении оно не кристаллизуется? Дело в том, что при его охлаждении вязкость возрастает очень быстро, и ионы не успевают перестроиться и образовать правильную кристаллическую решётку. Подобным же образом ведёт себя, например, глицерин, который трудно закристаллизовать (tпл=20°С). В стеклообразном состоянии можно получить даже металл, если его расплавить, а потом охладить с очень большой скоростью - миллионы градусов в секунду.
Тем не менее в специальных условиях стекло можно всё же получить и в кристаллическом состоянии. Такие материалы называются ситаллами. Они обладают ценными механическими, оптическими (в том числе цвет стекла ) и электрическими свойствами, которые можно целенаправленно менять, изменяя их химический состав.
Введение в расплав определённых элементов позволяет получить различный цвет и изменить его свойства. Например, чтобы цвет стекла измелился на зелёный или жёлтый, вводя в расплав ионы хрома или его оксиды. Цвет стекла - оранжевый - получают с помощью добавления серебра; синий цвет придаёт кобальт Co. Бутылочный цвет или изумрудно-зелёнй - придаёт железо, медь – голубой и синий. При внесении в расплав ионов золота оно приобретает кроваво-красный цвет. При добавлении в жидкое стекло ионов бора получают высокопрочное стекло , используемое в химических лабораториях.
Особыми механическими свойствами обладает хрусталь , который отличается от обыкновенного наличием ионов свинца и бария.
Разновидность стекла, содержащая значительное количество оксида свинца PbO, а также, возможно, окись бария BaO. Добавка оксида свинца увеличивает показатель преломления и дисперсию света в нём (с ювелирной точки зрения «игру цвета», «огонь»). Добавка оксида бария в основном увеличивает только показатель преломления. Добавка оксида свинца также увеличивает пластические свойства и, соответственно, возможности по обработке - огранке, резьбе и т.п.
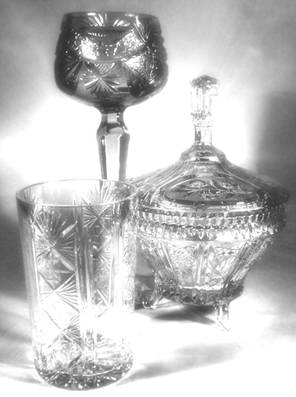
Огранка хрусталя , подобно огранке драгоценных камней, позволяет хрусталю в полной мере проявить свойства, обусловленные большим показателем преломления и дисперсией. Название было дано по аналогии с горным хрусталем . Изготавливают сплавлением оксида свинца PbO с кремнеземом, соединением натрия или калия (содой или поташoм) и малыми добавками других оксидов. Свинцово-калиево-силикатные стекла дороже известковых, однако они легче плавятся и проще в изготовлении. Это позволяет использовать высокие концентрации PbO и низкие - щелочного металла - без ущерба для легкоплавкости. Высокое содержание PbO дает высокие значения показателя преломления и дисперсии - двух параметров, весьма важных в некоторых оптических приложениях. Те же самые характеристики придают свинцовым стеклам сверкание и блеск, украшающие самые утонченные изделия столовой посуды и произведения искусства.
Это свинцово-силикатное стекло, содержащее 13-30 % и более окислов свинца и до 17 % окислов калия. Из хрусталя производят высококачественную посуду и декоративные изделия. Оно обладает повышенной массой, прозрачностью, лучепреломляемостью и блеском, но меньшей термостойкостью по сравнению с другими его видами. Благодаря содержанию свинца и определённому подбору углов, образуемых гранями изделия из хрусталя отличаются необыкновенно яркой, многоцветной игрой света. Обладают красивым звоном. Хрусталем называется также высококачественное венецианское и чешское стекло . Стиль художественного стекла (хрусталь) - торжественно-парадный, сувенирно-подарочный. Способы обработки изделий из хрусталя: гравировка, огранка, резьба, шлифовка