தொழிற்சாலையில் டயர்களை வாங்குவது எப்படி. வாகன டயர் உற்பத்தி தொழில்நுட்பம்
உலகின் முதல் ரப்பர் புதிய டயர் 1846 இல் ராபர்ட் வில்லியம் தாம்சன் என்பவரால் தயாரிக்கப்பட்டது, ஆனால் அவரது கண்டுபிடிப்பு வெகுஜன உற்பத்தியாக உருவாக்கப்படவில்லை. ஸ்காட்லாந்து வீரர் ஜான் டன்லப் தனது 10 வயது மகனின் ட்ரைசைக்கிள் அகலமான வளையங்களை தோட்டக் குழாயிலிருந்து சக்கரத்தில் ஏற்றி அவற்றை ஊதிப் பெருக்கும் யோசனையை 1887 ஆம் ஆண்டில் மீண்டும் அறிமுகப்படுத்தியபோதுதான் நியூமேடிக் டயர் பற்றிய யோசனை மீண்டும் அறிமுகப்படுத்தப்பட்டது. காற்றுடன். ஏற்கனவே 1890 ஆம் ஆண்டில், இளம் பொறியியலாளர் சாட் கிங்ஸ்ட்ன் வெல்ட்ச் அறையை டயரிலிருந்து பிரிக்கவும், டயரின் விளிம்புகளில் கம்பி வளையங்களைச் செருகவும் மற்றும் விளிம்பில் வைக்கவும் முன்மொழிந்தார், இது பின்னர் மையத்தை நோக்கி ஒரு மந்தநிலையைப் பெற்றது. அதே நேரத்தில், ஆங்கிலேயர் பார்ட்லெட் மற்றும் பிரெஞ்சுக்காரர் டிடியர் டயர்களை ஏற்றுவதற்கும் இறக்குவதற்கும் மிகவும் ஏற்றுக்கொள்ளக்கூடிய முறைகளைக் கண்டுபிடித்தனர். இவை அனைத்தும் ஒரு காரில் நியூமேடிக் டயர்களைப் பயன்படுத்துவதற்கான சாத்தியத்தை தீர்மானித்தன.
1. டயர்களின் உற்பத்திக்கான முக்கிய பொருட்கள் ரப்பர் ஆகும், இது இயற்கை மற்றும் செயற்கை ரப்பர்கள் மற்றும் தண்டு ஆகியவற்றிலிருந்து தயாரிக்கப்படுகிறது. தண்டு துணி உலோக நூல்கள் (உலோக தண்டு), பாலிமர் மற்றும் ஜவுளி நூல்களால் செய்யப்படலாம். ஒரு டயர் ஒரு சடலம், பெல்ட் அடுக்குகள், ஜாக்கிரதை, மணி மற்றும் பக்கச்சுவர் ஆகியவற்றைக் கொண்டுள்ளது.
2. புகைப்படத்தில் நீங்கள் எதிர்கால தண்டு பார்க்கிறீர்கள்.
3. சுத்தப்படுத்தப்படாத ரப்பர் மிகவும் ஒட்டும் தன்மையுடையது, எனவே அது ஒரு சிறப்புப் பொருளின் புறணியுடன் ஸ்பூல்களில் காயப்படுத்தப்படுகிறது, பின்னர் அதை எளிதில் அவிழ்க்க அனுமதிக்கிறது.
4. அத்தகைய பாபின்களில் உள்ள வெற்றிடங்கள் கிடங்கிற்கு அனுப்பப்படுகின்றன. எண் பலகைகள் தண்டு அகலத்தின் பரிமாணங்களாகும்.
5. இங்குதான் டிரெட் உற்பத்தி தொடங்குகிறது. ரப்பர் துண்டு இயந்திரத்தில் செலுத்தப்படுகிறது, அங்கு அது எதிர்கால ஜாக்கிரதையாக வெளியேற்றப்படுகிறது.
6. டயர் அளவின் விரைவான காட்சி மதிப்பீட்டிற்காக ஜாக்கிரதையாக வண்ண-குறியிடப்பட்டுள்ளது.
7. பீட் டயர் சக்கர விளிம்பில் இறுக்கமாக உட்கார அனுமதிக்கிறது. இதற்காக, மணி மோதிரங்கள் மற்றும் பிசுபிசுப்பான காற்று புகாத (டியூப்லெஸ் டயர்களுக்கு) ரப்பரின் உள் அடுக்கு ஆகியவை வடிவமைக்கப்பட்டுள்ளன.
8. இந்த spools இருந்து கம்பி இயந்திரம் செல்கிறது, அது ரப்பர் மூடப்பட்டிருக்கும்.
9. இந்த இயந்திரத்தில், ரப்பர் செய்யப்பட்ட கம்பி தேவையான விட்டம் மற்றும் வட்டங்களில் வெட்டப்படுகிறது.
10. முழு மணிகளின் உற்பத்திக்கு அடிப்படையான மணி வளையங்கள் இவை.
11. பலகை இங்கே போகிறது. இந்த செயல்முறையின் வீடியோவை கீழே காணலாம்.
12. மிகவும் சுவாரஸ்யமான நிலை- டயர் சட்டசபை. தேவையான அனைத்து பணியிடங்களும் இந்த இயந்திரத்திற்கு வழங்கப்படுகின்றன.
13. "ரோபோட்களுக்கு மகிமை!" வகுப்பிலிருந்து இயந்திரம். சேகரிப்பாளர் மணி மோதிரங்களை மட்டுமே தொங்கவிடுகிறார்.
14. பின்னர் சாதனம் எல்லாவற்றையும் தானே செய்கிறது: இது டயரின் அனைத்து கூறுகளையும் சேகரித்து, ஒரு பிரேக்கருடன் ஓடுதளத்தின் கீழ் காற்றுடன் பணிப்பகுதியை உயர்த்துகிறது.
கார் டயர்கள் நமக்கு மிகவும் பரிச்சயமான விஷயமாகும், அவற்றின் உற்பத்தியின் சிக்கலைப் பற்றி நாம் சிந்திக்கவே இல்லை. ஒரு இயந்திரத்தில் பஸ் நிறுவப்படுவதற்கு முன், பல செயல்முறைகள் நடைபெறுகின்றன. ஒவ்வொரு டயரின் உருவாக்கத்திலும், ஆலையின் சாதாரண தொழிலாளர்கள் மட்டுமல்ல, பல விஞ்ஞானிகளும் ஈடுபட்டுள்ளனர்.
ஆராய்ச்சி மையத்திலிருந்து கார் உரிமையாளர்களுக்கு புதிய டயரின் பாதை
பெரிய நிறுவனங்களில் பல ஆயிரம் ஊழியர்கள் உள்ளனர், அவர்களில் சிலர் மேம்பட்ட பட்டம் பெற்றவர்கள். அவர்களின் முக்கிய பணி, ஒரு புதிய வகை ஜாக்கிரதையாக கொண்டு வர வேண்டும் தோற்றம்சாலை, கார் கையாளுதல், பெட்ரோலின் பொருளாதார நுகர்வு, சத்தம் குறிகாட்டிகள் ஆகியவற்றில் ஒட்டுதல் தரத்தை சார்ந்துள்ளது. ரப்பரின் கலவையும் இங்கே முக்கியமானது, இது கட்டமைப்பின் ஆயுளை பாதிக்கிறது.
கிட்டத்தட்ட அனைத்து வளர்ச்சிகளும் சிறப்பு கணினி நிரல்களில் மேற்கொள்ளப்படுகின்றன. ஆராய்ச்சி மையத் தொழிலாளர்கள் டயரின் நடத்தையை உருவகப்படுத்தி, விருப்பத்தைத் தேர்வு செய்கிறார்கள் நல்ல பண்புகள்... பின்னர் சோதனை மாதிரிகள் தயாரிக்கப்பட்டு களத்தில் சோதிக்கப்படுகின்றன. ஒரு புதிய டயர் அதே வகுப்பின் மற்ற மாடல்களை விட சிறந்த முடிவுகளைக் காட்டினால், அது தொடர் உற்பத்தியில் வைக்கப்படுகிறது. பூர்வாங்க திருத்தங்கள் செய்யலாம்.
கார் டயர் உற்பத்தியின் நிலைகள்
ஒவ்வொரு வாகன அக்கறையும் அதன் சொந்த உற்பத்தி நுணுக்கங்களைக் கொண்டுள்ளது, அதை வெளியிட விரும்பவில்லை. இருப்பினும், அடிப்படை செயல்முறைகள் மற்றும் அவற்றின் வரிசை ஒத்தவை.
ரப்பர் கலவை உற்பத்தி
ஒவ்வொரு நிறுவனத்திற்கும் கலவையின் கலவை வேறுபட்டது. ஆயுள் மற்றும் ஒட்டுதலுக்கு இடையே உகந்த சமநிலையை வழங்க வேதியியலாளர்கள் கூறுகளின் விகிதாச்சாரத்தையும் பட்டியலையும் தேர்ந்தெடுக்கின்றனர். ரப்பர் கலவையின் முக்கிய கூறுகள்:
- ரப்பர்- எந்த ரப்பரின் அடிப்படையும். இயற்கை அல்லது செயற்கை தோற்றம் பயன்படுத்தப்படலாம். பல வெளிநாட்டு உற்பத்தியாளர்கள் ரஷ்யாவிலிருந்து ரப்பரை வாங்குகிறார்கள்.
- தொழில்துறை சூட்... மற்றொரு வழியில், இது கார்பன் கருப்பு என்றும் அழைக்கப்படுகிறது. இது கண்ணீர் மற்றும் சிராய்ப்பு எதிர்ப்பை மேம்படுத்துகிறது. கார்பன் கருப்பு வல்கனைசேஷன் போது மூலக்கூறு பிணைப்பு பொறுப்பு மற்றும் ரப்பர் ஒரு சிறப்பு நிறம் கொடுக்கிறது.
- சிலிசிக் அமிலம்... அமெரிக்க மற்றும் ஐரோப்பிய நிறுவனங்கள், தங்கள் பிரதேசங்களில் கார்பன் பிளாக் உற்பத்திக்கு போதுமான அளவு இயற்கை எரிவாயு இல்லாததால், சிலிசிக் அமிலத்தைப் பயன்படுத்தத் தொடங்கின. சிலிசிக் அமிலம் தொழில்துறை கார்பன் கருப்பு நிறத்தை முழுமையாக மாற்ற முடியாது, ஏனெனில் இது ரப்பருக்கு அதிக வலிமையைக் கொடுக்காது. ஆனால் அது ஈரமான பரப்புகளில் பிடியை மேம்படுத்துகிறது. வெளிநாட்டில், இந்த பொருள் ரப்பரில் சுற்றுச்சூழல் நட்பு கூறுகளாக நிலைநிறுத்தப்பட்டுள்ளது. டயர் செயல்பாட்டின் போது சிலிசிக் அமிலம் குறைவாக துடைக்கப்படுகிறது மற்றும் நிலக்கீல் மீது கருப்பு புள்ளிகளை விடாது.
- எண்ணெய்கள் மற்றும் பிசின்கள்... முடிக்கப்பட்ட தயாரிப்புக்கு தேவையான அளவு கடினத்தன்மையை வழங்க அவை கலவையில் சேர்க்கப்பட்டுள்ளன.
- வல்கனைசேஷன் ஆக்டிவேட்டர்கள். இதில் சல்பர், துத்தநாக ஆக்சைடு, ஸ்டீரிக் அமிலங்கள் அடங்கும். அவை வல்கனைசேஷன் செயல்முறைக்கு துவக்கிகளாகவும் வினையூக்கிகளாகவும் செயல்படுகின்றன, மேலும் பாலிமர் மூலக்கூறுகளுக்கு இடையில் ஒரு இடஞ்சார்ந்த வலையமைப்பை உருவாக்குகின்றன.
டயர் கூறுகளின் உற்பத்தி
பஸ் கூறுகள் இரண்டு முக்கிய குழுக்களாக பிரிக்கப்பட்டுள்ளன, அவை இணையாக உற்பத்தி செய்யப்படுகின்றன. முதல் குழுவில் பாதுகாவலர், ஹெர்மீடிக் அடுக்கு, பக்கச்சுவர்கள், இரண்டாவது - மணி மோதிரங்கள், உலோக தண்டு, ஜவுளி தண்டு ஆகியவை அடங்கும்.
கார் டயர் அசெம்பிளி
ஒரு பிரேக்கர், ஒரு நைலான் பேண்டேஜ் மற்றும் ஒரு பாதுகாவலர் ஆகியவை தொடர்ச்சியாக ஒரு டிரம்மில் காயப்படுத்தப்படுகின்றன. இரண்டாவது டிரம்மில், மணி வளையம் மற்றும் உச்சம் ஆகியவை ஹெர்மீடிக் அடுக்கு மற்றும் பக்கச்சுவர்களுடன் இணைக்கப்பட்டுள்ளன. இரண்டு பகுதிகளும் இணைந்த பிறகு, இதன் விளைவாக ஒரு "மூல" டயர் ஆகும். அடுத்த செயல்முறைக்கு அவள் முற்றிலும் தயாராக இருக்கிறாள்.
குணப்படுத்துதல்
ஒரு சிறப்பு நிறுவலில், "ஈரமான" டயர் அதிக வெப்பநிலை (170-205 டிகிரி செல்சியஸ்) மற்றும் 22 பட்டையின் அழுத்தத்தின் செல்வாக்கின் கீழ் உயர்த்தப்பட்டு செயலாக்கப்படுகிறது. வெப்பநிலை மற்றும் அழுத்த மதிப்புகள் டயர் வகையைப் பொறுத்தது மற்றும் காட்டப்படும் அளவுருக்களிலிருந்து வேறுபடலாம். இறுதி கட்டத்தில், அனைத்து கூறுகளும் ஒரு பிரிக்க முடியாத முழுதாக இணைக்கப்படுகின்றன. வல்கனைசேஷன் நேரம் சுமார் 10 நிமிடங்கள் ஆகும். அதன் பிறகு, டயர் பழக்கமான தோற்றத்தைப் பெறுகிறது.
தர கட்டுப்பாடு
தயார் கார் டயர்கள்ஆய்வு அனுபவம் வாய்ந்த ஊழியர்கள்பின்னர் தானியங்கி இயந்திரங்களை சரிபார்க்கவும். குறைபாடுகள் உள்ள தயாரிப்புகள் அகற்றப்பட்டு நுகர்வோரை சென்றடையாது. சில நிலைகளின் முடிவில் தரக் கட்டுப்பாடும் ஏற்படலாம், உதாரணமாக, ரப்பர் கலவையின் கலவை சரிபார்க்கப்படுகிறது. முழு தொழில்நுட்ப செயல்முறையும் முக்கியமாக இயந்திரங்கள் மற்றும் கணினிகளால் மேற்கொள்ளப்படுகிறது. நபர் முக்கியமாக இரும்பு உதவியாளர்களின் வேலையைப் பின்பற்றுகிறார்.
முடிவுரை
புதிய டயர்களின் உருவாக்கம் மற்றும் வடிவமைப்பு மிகவும் சிக்கலான தொழில்நுட்ப செயல்முறையாகும். ஒவ்வொரு டயரின் தயாரிப்பிலும் நிறைய வேலை மற்றும் ஆராய்ச்சி ஈடுபட்டுள்ளது. தொழிற்சாலையில், ஒரு டயர் ஒரு ரப்பர் கலவையை உருவாக்குவது முதல் வல்கனைசேஷன் வரை பல நிலைகளில் செல்கிறது. நுகர்வோரை சென்றடையும் முன், ஒவ்வொரு டயரின் தரமும் மனித மற்றும் ரோபோ இயந்திரம் மூலம் சரிபார்க்கப்படுகிறது.
டயர் தொழில்நுட்பம் ஒரு சிறப்பு மூலம் அதன் வளர்ச்சியுடன் தொடங்குகிறது கணினி நிரல்டிரெட் மற்றும் டயரின் சுயவிவரத்தின் பல்வேறு மாற்றங்களை வரைதல். திட்டத்தின் உதவியுடன், வெவ்வேறு சூழ்நிலைகளில் சாலையில் உள்ள டயரின் ஒவ்வொரு மாறுபாட்டின் நடத்தையும் கணக்கிடப்படுகிறது. அதன் பிறகு, உருவகப்படுத்தப்பட்ட சாலை சோதனைகளில் சிறப்பாகச் செயல்பட்ட அந்த டயர்கள் ஒரு இயந்திரத்தில் கையால் வெட்டப்பட்டு உண்மையான சாலை நிலைகளில் சோதிக்கப்படுகின்றன. சோதனை செய்யப்பட்ட ஒவ்வொரு டயரின் தொழில்நுட்ப குறிகாட்டிகளும் அதே வகுப்பின் தற்போதைய டயர்களின் சிறந்த குறிகாட்டிகளுடன் ஒப்பிடப்படுகின்றன, தேவைப்பட்டால், அவை சுத்திகரிக்கப்படுகின்றன மற்றும் தயாரிப்பு வெகுஜன உற்பத்தியில் தொடங்கப்படுகிறது.
கார் டயர் உற்பத்தியின் நிலைகள்
1. ரப்பர் கலவை உற்பத்தி
எந்தவொரு டயரையும் உருவாக்குவதற்கான முதல் கட்டம் ஒரு ரப்பர் கலவையை உருவாக்குவதாகும், அதன் கலவை ஒவ்வொரு உற்பத்தி நிறுவனத்திற்கும் தனிப்பட்டது மற்றும் கடுமையான இரகசியமாக வைக்கப்படுகிறது. டயர்கள் சார்ந்து இருக்கும் ரப்பரின் தரத்தில் துல்லியமாக இருப்பதே இதற்குக் காரணம். விவரக்குறிப்புகள், எப்படி:
- சாலைக்கு ஒட்டும் நிலை;
- நம்பகத்தன்மை;
- வேலை வளம்.
மூலப்பொருட்கள் மற்றும் நுகர்பொருட்கள்
டயர் தொழில்நுட்பத்திற்கு பல்வேறு கூறுகள், பொருட்கள் மற்றும் தேவை இரசாயன கலவைகள்இது இல்லாமல் அது சாத்தியமற்றது. இந்த கட்டுரையில், இந்த கூறுகளில் மிக அடிப்படையானவற்றை மட்டுமே பட்டியலிடுவோம்.
இவை அனைத்தும் வேதியியலாளர்களின் பணியால் அடையப்படுகின்றன, அவர்கள் தங்கள் சொந்த அனுபவம் மற்றும் கணினி தரவுகளுக்கு ஏற்ப கூறுகளையும் அவற்றின் உள்ளடக்கத்தையும் ரப்பரில் தேர்ந்தெடுத்து இணைக்கிறார்கள். ஒரு விதியாக, ரப்பரின் தரம் கூறுகளின் சரியான அளவைப் பொறுத்தது, ஏனெனில் அதன் கலவை யாருக்கும் இரகசியமாக இல்லை மற்றும் பின்வரும் கூறுகளை உள்ளடக்கியது:
- ரப்பர் கலவையின் அடிப்படையை உருவாக்கும் ரப்பர், இது செயற்கையாகவோ அல்லது அதிக விலை ஐசோபிரீனாகவோ இருக்கலாம். நடைமுறையில் காண்பிக்கிறபடி, ரஷ்ய ரப்பர் உலகில் மிகச் சிறந்ததாகக் கருதப்படுகிறது மற்றும் இன்னும் பிரபலமான வெளிநாட்டு உற்பத்தி நிறுவனங்களால் தங்கள் தயாரிப்புகளின் உற்பத்திக்கு பயன்படுத்தப்படுகிறது;
- தொழில்துறை சூட், இது கார்பன் கருப்பு, இது ரப்பருக்கு ஒரு சிறப்பியல்பு நிறத்தை அளிக்கிறது மற்றும் அதன் வலிமை மற்றும் உடைகள் எதிர்ப்பிற்கு பொறுப்பாகும், ஏனெனில் இது வல்கனைசேஷன் செயல்பாட்டின் போது மூலக்கூறு இணைப்பைச் செய்யும் சூட் ஆகும்;
- சிலிக்கிக் அமிலம், இது டயர்கள் தயாரிப்பில் கார்பன் கருப்புக்கு ஒப்பானது வெளிநாட்டு உற்பத்தியாளர்கள்மற்றும் ஈரமான சாலை மேற்பரப்புடன் டயரின் பிடியின் அளவை அதிகரிப்பது;
- எண்ணெய்கள் மற்றும் பிசின்கள், அவை துணை கூறுகள் மற்றும் ரப்பர் மென்மையாக்கிகளின் பாத்திரத்தை வகிக்கின்றன.
- வல்கனைசிங் முகவர்கள், குறிப்பாக சல்பர் மற்றும் வல்கனைசிங் ஆக்டிவேட்டர்கள்.
2. டயர் கூறுகளின் உற்பத்தி
டயர் உற்பத்தி தொழில்நுட்பம் டயர் கூறுகளின் உற்பத்தி போன்ற ஒரு உற்பத்தி நிலைக்கு வழங்குகிறது, இது போன்ற பல இணையான செயல்முறைகள்:
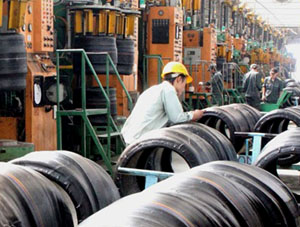
3. டயர் சட்டசபை மற்றும் வல்கனைசேஷன்
டயர் அசெம்பிளி என்பது உற்பத்தியின் மூன்றாவது கட்டமாகும், மேலும் இது ஒரு கட்டிட டிரம்மில் கர்காஸ், பீட் மற்றும் ட்ரெட் ஆகியவற்றின் அடுக்குகளை டயர் பக்கச்சுவர்களுடன் தொடர்ச்சியாக ஒன்றுடன் ஒன்று சேர்ப்பதன் மூலம் செய்யப்படுகிறது, அதைத் தொடர்ந்து வல்கனைசேஷன் செயல்முறை செய்யப்படுகிறது.
கார் டயர் உற்பத்தி தொழில்நுட்பம், வீடியோ ஆய்வு:
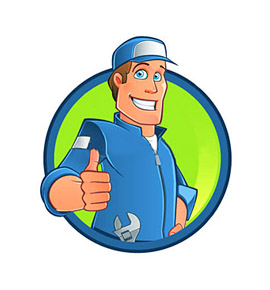
பல கார் உரிமையாளர்களுக்கு கார் டயர்களின் கட்டமைப்பைப் பற்றிய பொதுவான யோசனை உள்ளது, ஆனால் டயர்கள் எவ்வாறு தயாரிக்கப்படுகின்றன என்பதை சிலர் சொல்ல முடியும். மிகவும் பொதுவான யோசனை என்னவென்றால், ரப்பர் ஒரு வடிவத்தில் ஊற்றப்படுகிறது, அதில் இருந்து முடிக்கப்பட்ட தயாரிப்பு வெளியேற்றப்படுகிறது.
உண்மையில், இது அப்படியல்ல, மேலும் கார் டயர்கள் தயாரிப்பது ஒரு சிக்கலான உயர் தொழில்நுட்ப செயல்முறையாகும், இது அதிநவீன சிறப்பு உபகரணங்கள், கவனமாக தானியங்கு கட்டுப்பாடு மற்றும் அதிக தகுதி வாய்ந்த நிபுணர்களின் பங்கேற்பு தேவைப்படுகிறது.
கொஞ்சம் வரலாறு
முதல் ரப்பர் டயர் 1846 இல் ராபர்ட் வில்லியம் தாம்ஸனால் உருவாக்கப்பட்டது. அந்த நேரத்தில், அவரது கண்டுபிடிப்பில் யாரும் ஆர்வம் காட்டவில்லை, மேலும் அவர்கள் 40 ஆண்டுகளுக்குப் பிறகுதான் நியூமேடிக் டயர்களின் யோசனைக்குத் திரும்பினார்கள், 1887 ஆம் ஆண்டில் ஸ்காட்ஸ்மேன் ஜான் டன்லப் ஒரு நீர்ப்பாசன குழாயிலிருந்து வளையங்களை உருவாக்கும் யோசனையுடன் வந்தார். அவற்றைத் தன் மகனின் சைக்கிளின் சக்கரங்களில் ஏற்றி காற்றை செலுத்தினான்.
மூன்று ஆண்டுகளுக்குப் பிறகு, சார்லஸ் கிங்ஸ்டன் வெல்ட்ச் டியூப் மற்றும் டயரைப் பிரித்து, டயரின் விளிம்புகளில் கம்பி வளையங்களைச் செருகி, அவற்றை விளிம்பில் வைப்பதை முன்மொழிந்தார். அதே நேரத்தில், டயர்களை ஏற்றுவதற்கும் இறக்குவதற்கும் பகுத்தறிவு முறைகள் முன்மொழியப்பட்டன, இது கார்களில் ரப்பர் டயர்களைப் பயன்படுத்துவதை சாத்தியமாக்கியது.
டயர் உற்பத்தி செயல்முறை
அவை எதனால் ஆனவை
டயர்கள் உற்பத்தியில் பயன்படுத்தப்படும் முக்கிய பொருள் ரப்பர், இயற்கை அல்லது செயற்கை ரப்பரின் அடிப்படையில் தயாரிக்கப்படுகிறது. என்ன விகிதங்கள் மற்றும் எந்த வகையான ரப்பர் சேர்க்கப்படுகிறது என்பதைப் பொறுத்து, இறுதி முடிவு கோடை அல்லது குளிர்கால கார் டயர்கள் ஆகும்.
எனவே, ரப்பர் கலவையில் கோடை டயர்கள்முக்கியமாக செயற்கை ரப்பர் சேர்க்கப்படுகிறது, எனவே ரப்பர் மிகவும் கடினமானதாக மாறும், அணிய எதிர்ப்பு, அது அதிக வெப்பநிலையில் "மிதக்காது" மற்றும் சாலை மேற்பரப்பில் நம்பகமான ஒட்டுதலை வழங்குகிறது. குளிர்கால டயர்களை உருவாக்க, இயற்கை ரப்பர் சேர்க்கப்படுகிறது, இது ரப்பரை மென்மையாகவும் மீள்தன்மையுடனும் செய்கிறது. அதன் மூலம் குளிர்கால டயர்கள்மிகவும் கடுமையான உறைபனிகளில் கூட "டப்" செய்ய வேண்டாம்.
- ரப்பரைத் தவிர, பிளாஸ்டிசைசர்கள், கலப்படங்கள், கார்பன் கருப்பு, வல்கனைசிங் சேர்க்கைகள் போன்ற பல கூறுகள் ரப்பர் கலவையில் சேர்க்கப்படுகின்றன.
- ஒரு டயர் முழுவதுமாக பல கூறுகளைக் கொண்டுள்ளது: சடலம் அல்லது தண்டு, பெல்ட் அடுக்குகள், ஜாக்கிரதை, மணி மற்றும் பக்க பகுதி.
சட்டகம் எவ்வாறு தயாரிக்கப்படுகிறது
எதிர்கால டயரின் தண்டு உலோகம், ஜவுளி அல்லது பாலிமர் நூல்களால் க்ரீல் எனப்படும் சிறப்பு இயந்திரத்தில் செய்யப்படுகிறது. கம்பியின் பல ஸ்பூல்களிலிருந்து, இழைகள் ஒரே இடத்தில் ஒன்றிணைகின்றன. வி பொதுவான அவுட்லைன்கட்டுமானம் ஒரு தறியை ஒத்திருக்கிறது. பின்னர் பின்னப்பட்ட தண்டு எக்ஸ்ட்ரூடருக்குள் நுழைகிறது, அங்கு அது ரப்பரைஸ் செய்யப்படுகிறது.
முடிக்கப்பட்ட சடலம் பின்னர் வெவ்வேறு பரிமாணங்களின் டயர்களின் உற்பத்திக்காக வெவ்வேறு அகலங்களின் கீற்றுகளாக வெட்டப்படுகிறது. மற்றும் சேமிப்பு மற்றும் போக்குவரத்துக்காக ரீல்களில் சுருட்டப்பட்டது. சுத்தப்படுத்தப்படாத ரப்பர் மிகவும் ஒட்டும் தன்மையுடன் இருப்பதால், சடலத்திற்கு சேதம் ஏற்படுவதைத் தடுக்க அடுக்குகளுக்கு இடையில் ஸ்பேசர்கள் செருகப்படுகின்றன.
பாதுகாவலர் எவ்வாறு தயாரிக்கப்படுகிறது
உற்பத்தியின் அடுத்த கட்டம் ஒரு ஜாக்கிரதையை உருவாக்குவதாகும். ரப்பராக்கப்பட்ட தண்டு டேப் இயந்திரத்தில் செலுத்தப்படுகிறது, இது வெளியேற்றுவதன் மூலம் அதை ஒரு ஜாக்கிரதையாக மாற்றுகிறது. எதிர்கால டயரின் பரிமாணத்தை தொழிலாளர்கள் பார்வைக்கு விரைவாக தீர்மானிக்க முடியும், வண்ணக் கோடுகள் வண்ணப்பூச்சுடன் ஜாக்கிரதையாக வரையப்படுகின்றன.
பக்க பகுதி
டயரின் பீட் ஒரு மணி வளையம் மற்றும் பிசுபிசுப்பான காற்று புகாத ரப்பர் அடுக்கு ஆகியவற்றைக் கொண்டுள்ளது. டயர் மணிகளின் உற்பத்தி உலோக கம்பியை ரப்பர்மயமாக்குவதன் மூலம் தொடங்குகிறது, அதன் பிறகு அது விளிம்பின் தேவையான ஆரம் கீழ் முறுக்கப்பட்டு வட்டங்களில் வெட்டப்படுகிறது. அதன் பிறகு, சட்டசபை இயந்திரத்தில் மேற்கொள்ளப்படுகிறது. இந்த செயல்முறை பற்றிய கூடுதல் விவரங்களை வீடியோவில் காணலாம்.
சட்டசபை
இறுதி கட்டம் முடிக்கப்பட்ட டயரின் அசெம்பிளி ஆகும். இது இயந்திரத்தில் மேற்கொள்ளப்படுகிறது, இது அனைத்து முடிக்கப்பட்ட கூறுகளையும் பெறுகிறது. இயந்திரம் இரண்டு தொழிலாளர்களால் சேவை செய்யப்படுகிறது: ஒரு அசெம்பிளர் மற்றும் ஒரு ரீசார்ஜர்.
முதல் ஒரு மணி மோதிரங்கள் தொங்குகிறது, மற்றும் இரண்டாவது ஒரு கூறுகளுடன் சுருள்கள் செருகும். அதன் பிறகு, இயந்திரம் தானாகவே அனைத்தையும் செய்கிறது: இது பகுதிகளை ஒன்றாக இணைக்கிறது மற்றும் ஒரு பிரேக்கர் மூலம் பாதுகாப்பாளரின் கீழ் காற்றுடன் பணிப்பகுதியை உயர்த்துகிறது. ஏறக்குறைய முடிக்கப்பட்ட டயர் எடையும் குறைபாடுகளும் உள்ளதா என பரிசோதிக்கப்படுகிறது. இந்த செயல்முறையை நீங்கள் வீடியோவில் பார்க்கலாம்.
குணப்படுத்துதல்
உற்பத்தியின் கடைசி நிலை வல்கனைசேஷன் ஆகும். டயர் சூடான நீராவியுடன் 15 பட்டையின் அழுத்தத்திலும், சுமார் 200 டிகிரி செல்சியஸ் வெப்பநிலையிலும் சிகிச்சையளிக்கப்படுகிறது. இதன் விளைவாக, ரப்பர், சூட் மற்றும் அனைத்து வகையான சேர்க்கைகளும் சின்டர் செய்யப்படுகின்றன, மேலும் அச்சுகளைப் பயன்படுத்தி டயரின் மேற்பரப்பில் ஒரு ஜாக்கிரதையான முறை மற்றும் கல்வெட்டுகள் பயன்படுத்தப்படுகின்றன. முடிக்கப்பட்ட டயர்கள் தேவையான அனைத்து விவரக்குறிப்புகளையும் பூர்த்தி செய்வதை உறுதிப்படுத்த சோதிக்கப்படுகின்றன.